Industrielle KI erlaubt die zweite Welle der Digitalisierung
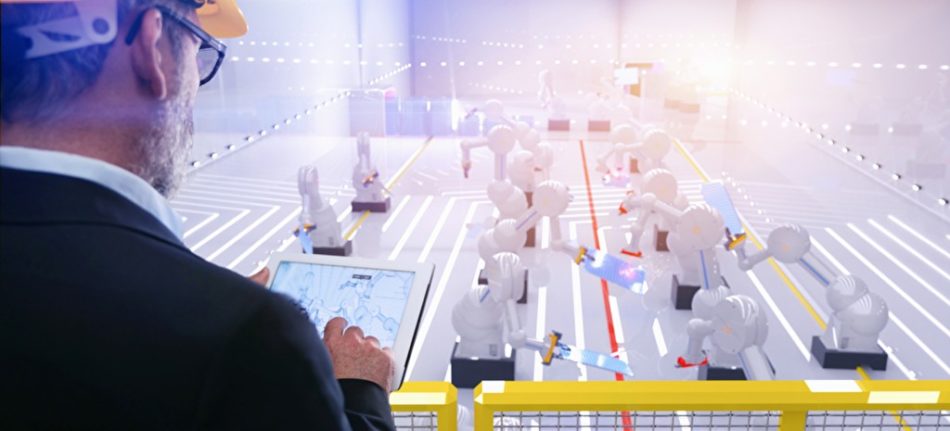
Foto: PantherMedia / aa-w
Vor zehn Jahren hat der DFKI-Gründungsdirektor Wolfgang Wahlster zusammen mit Henning Kagermann (Acatech) und Wolf-Dieter Lukas (BMBF) gegenüber den VDI nachrichten zum ersten Mal über Industrie 4.0 berichtet. So fällt seine Bilanz heute aus.
VDI nachrichten: Was von der Konzeption einer Industrie 4.0, die Sie zusammen mit Herrn Kagermann und Herrn Lukas am 1. 4. 2011 publizierten, ist heute schon verwirklicht?
Wahlster: Das Internet der Dinge und darauf aufsetzende cyber-physische Systeme sind in modernen Fabriken heute Realität. Die digitale Konnektivität zwischen allen Maschinen, Werkzeugen und Werkstücken und den Facharbeitern hat auch in Bestandsfabriken große Fortschritte gemacht. Die sensorische Aufrüstung aufgrund neuer preiswerter Sensoren und deren drahtlose Anbindung schreitet stetig voran, sodass immer mehr Produktionsschritte durch Multisensorfusion in Echtzeit u. a. zur Qualitätskontrolle überwacht werden können.
Digitale Zwillinge werden genutzt
Ausgehend von unseren frühen Arbeiten ab 2008 zu aktiven digitalen Objektgedächtnissen, werden auch immer mehr digitale Zwillinge realisiert. Wir nähern uns also dem Ziel, dass es für jedes physische Objekt ein digitales Abbild gibt, das automatisch und in Echtzeit aktualisiert und für Steuerungsimpulse genutzt werden kann.
Neue Fabriken werden heute stets als wandelbare Fabriken konzipiert – die Zeiten, in denen eine Fabrik nur für eine spezielle Produktlinie konzipiert wird, sind endgültig vorbei. Beispielsweise muss jede Fabrik für Fahrzeugmotoren bei der Volatilität der Mobilitätswende mit geringem zeitlichen und finanziellen Aufwand auf alternative Antriebsstränge umstellbar sein.
Die traditionelle Automatisierungspyramide wurde zugunsten heterarchischer Service-orientierter Architekturen aufgelöst, die auch die dezentrale Produktion unterstützen.
Was bedeutet das für die Praxis?
Heute gibt es etliche neu errichtete „Smart Factories“, die viele Grundprinzipien von Industrie 4.0 bereits umsetzen: Plug & Produce, taktunabhängige Matrix-Produktionsarchitekturen mit konfigurierbaren Produktionszellen und kurzen Umrüstzeiten auch für kleinste Losgrößen mit großem Produktindividualisierungsgrad, variable Intralogistik kombiniert mit Echtzeitproduktionsplanung sowie lokationsbasierte Dienste für alle Werker, die Betriebsmittel und die entstehenden Produkte.
Die Positionsbestimmung in Fabrikhallen ist mithilfe KI-basierter visueller SLAM-Verfahren für mobile Systeme wie autonome Gabelstapler stark verbessert worden. Durch die hochparallele Ausführung neuronaler Verfahren auf sehr leistungsfähigen Grafikkarten – sogenanntes GPU-Computing – wurde die notwendige Erkennung von Landmarken signifikant verbessert, um eine freie Navigation mobiler Roboter zu ermöglichen.
Allerdings sind wir weit davon entfernt, dass in allen Unternehmen und Branchen Industrie 4.0 umgesetzt ist.
Konnte das 2011 verkündete Ziel, dass Deutschland bis zum Jahr 2020 Leitanbieter für Komponenten zur Realisierung cyber-physischer Produktionssysteme sein wird, erreicht werden?
Ja, unsere klassischen Fabrikausrüster wie Siemens, Bosch-Rexroth und ABB, aber noch stärker die vielen Hidden Champions aus dem Mittelstand waren die ersten Lösungsanbieter und haben immer noch einen Vorsprung von ein bis zwei Jahren. Sie werden weltweit keine Smart Factory finden, in der nicht eine Vielzahl von Software- und Hardwarekomponenten von deutschen Firmen stammt.
Und wie sieht es mit der US-Industrie aus, die mit dem Industrial Internet Consortium lange als ernster Konkurrent für die Deutsche Plattform Industrie 4.0 betracht wurde?
Der Angriff amerikanischer Unternehmen mit dem „Industrial Internet“ war zu kurz gesprungen, weil die reine Aufrüstung der Vernetzungs- und Kommunikationsinfrastruktur zwar eine Voraussetzung, aber keineswegs schon die Lösung für Industrie 4.0 darstellt. Auch IoT-Plattformen sind ohne semantisch codiertes Domänenwissen von exzellenten Ingenieuren und Facharbeitern, intelligente Steuerungen und digitale Zwillinge noch keine Lösungen für disruptive Fabrikmodelle.
Es braucht mehr als nur IoT-Plattformen
Noch wichtiger sind die Lösungen zum Retrofitting von Bestandsfabriken mit der Nachrüstung vernetzter IoT-Boxen, verteilter Sensorik und intelligenten Leitständen auf der Basis digitaler Zwillinge. Die digitale Veredelung hochpräziser und robuster klassischer Fertigungsanlagen ist eine Spezialität, die deutsche Mittelständler zum stark nachgefragten Lieferanten besonders in China gemacht haben.
Auch mobile Tablets, Smartphones, Smartwatches und Datenbrillen haben eine neue Generation von werker-individuellen kognitiven Assistenzsystemen ermöglicht, die schon heute die Produktivität, Produktqualität, Arbeitszufriedenheit, Sicherheit und Transparenz signifikant gesteigert haben, sodass der Mensch weiterhin im Mittelpunkt steht, lebenslang weiterlernt, keinen Kontrollverlust empfindet und mehr Freude an der Arbeit hat.
Wie wurde Industrie 4.0 allgemein im Ausland aufgenommen?
Der Begriff hat sich rasend viral ausgebreitet und wird heute wie die Begriffe „Kindergarten“ und „Autobahn“ mit Deutschland assoziiert. Industrie 4.0 wird als deutscher Exportschlager wahrgenommen, der in Wirtschaft, Wissenschaft und Politik eine weltweite Aufmerksamkeit und Anerkennung erfahren hat. Damit haben wir in der Hightechwelt erstmals wieder ein innovatives Konzept aus Deutschland international etablieren können, nachdem diese über viele Jahre meist aus Amerika oder Asien kamen.
In den letzten zehn Jahren haben sich 100 000 Publikationen, 10 000 Konferenzen und 1000 Projektkonsortien mit der technisch-wissenschaftlichen Umsetzung von Industrie 4.0 beschäftigt, sodass man heute mehr als 25 Mio. Internetverweise zu dem Begriff findet.
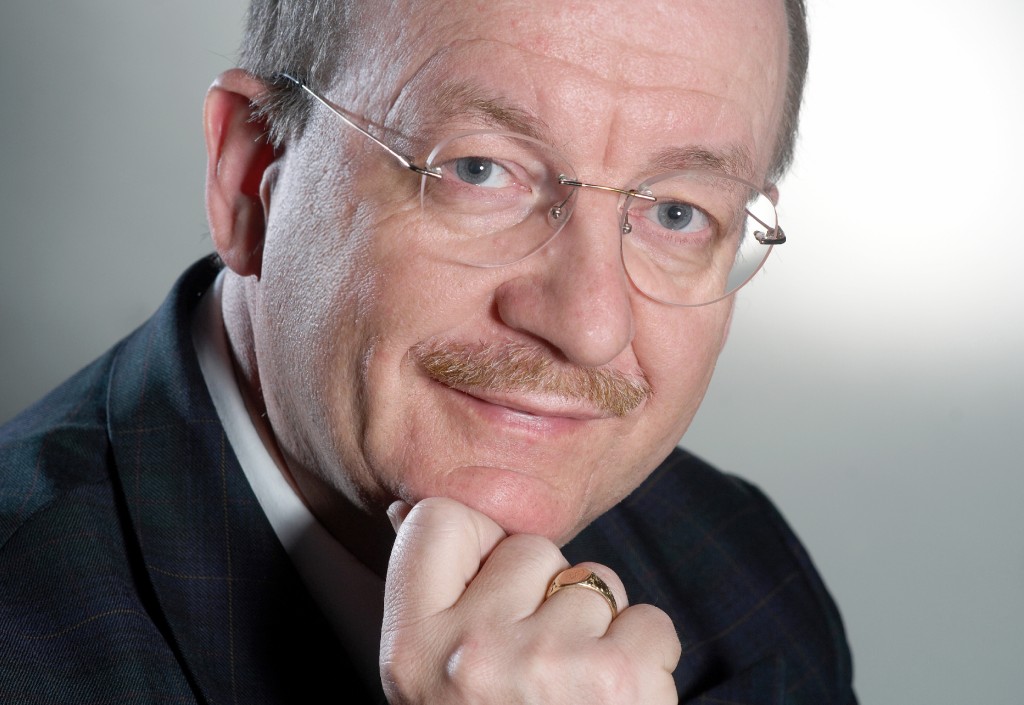
In Europa wurde neben großen Ländern wie in Frankreich auch in kleinen Ländern wie Tschechien, in Portugal, dem Baskenland, Finnland und den Niederlanden das Konzept rasch aufgegriffen und oftmals zunächst mit Tochtergesellschaften deutscher Unternehmen umgesetzt. So arbeiten beispielsweise I4.0-Zentren wie CIIRC/RICAIP in Prag eng mit Skoda/VW in Tschechien und das DTx CoLab in Porto eng mit Bosch in Portugal zusammen.
Starkes Engagement in China
China investiert derzeit sehr gezielt, um mit Industrie 4.0 seine Produktion, die vor einigen Jahren noch auf der Ebene von Industrie 2.0 arbeitete, an die Weltspitze zu führen. Japan ist dabei aber schon weiter, weil dort das neue Paradigma schneller und tiefer verstanden wurde und auch Korea holt auf.
In den USA wurde erst später und nach dem Fehlstart aufgrund der zunächst einseitigen Fokussierung auf das „industrielle Internet“ die volle Breite und Tiefe des Paradigmenwechsels von Industrie 4.0 erkannt und grundlegende Arbeiten dazu begonnen.
Welche neuen Technologietrends werden die nächsten zehn Jahre der vierten industriellen Revolution beeinflussen?
Fünf neue Megatrends sind dafür entscheidend: die industrielle KI, das Edge-Computing bis hin zur Edge-Cloud, 5G in der Fabrik, die Team-Robotik, autonome Intralogistiksysteme sowie vertrauenswürdige Dateninfrastrukturen, wie sie Gaia-X bereitstellen soll.
Mit der industriellen KI wird eine zweite Welle der Digitalisierung der Produktion möglich. Die erste Welle, die alle Daten der Produktion und der Lieferketten digital und mobil über Cloud-Systeme verfügbar macht, ist weitestgehend abgeschlossen.
Nun können diese digitalen Daten aber durch KI-Systeme analysiert und im Kontext interpretiert werden, sodass sie für neue Wertschöpfungsketten und innovative Geschäftsmodelle aktiv genutzt werden können. Mit digitalen Trainingsdaten für maschinelle Lernsysteme können KI-Systeme nicht nur zur bereits weitverbreitenden vorausschauenden Wartung, sondern immer mehr zur inkrementellen Qualitätskontrolle – meist über Videosensorik – benutzt werden.
Null-Fehler-Produktion durch KI
Damit wird in der nächsten Phase von Industrie 4.0 eine KI-basierte Null-Fehler-Produktion angestrebt. Die Selbstlernfähigkeit und modulare Langzeitautonomie werden die neue Generation von Smart Factories auszeichnen und neben einer extremen Flexibilität auch eine hohe Produktionsrobustheit, Arbeitssicherheit und hohes Maß an Ressourcenschonung garantieren. Eine fähigkeitsorientierte Produktionsarchitektur sichert die Erweiterbarkeit und Wandlungsfähigkeit auf der nächsten Stufe von Industrie 4.0 ab.
Mit privaten 5G-Campusnetzen können Edge-Devices mit der hohen Bandbreite und garantiert geringer Latenzzeit von 5G zu einer lokalen Edge-Cloud zusammengeschaltet werden, die dann den Echtzeitanforderungen in der Fabrik genügt.
Hybride Teams von Werkern und kollaborativen Robotern mit verschiedenen Fähigkeiten führen zu einer neuen Form der Team-Robotik, in der Mensch-Maschine-Interaktion unter Führung des menschlichen Fachpersonals im Mittelpunkt steht. Dabei wird Hand in Hand mit Robotern zusammenarbeitet, um im Team komplexe Fertigungsaufgaben zu lösen.
Wie müssen die Infrastrukturen für die unterschiedlichen Branchen aussehen?
Bei den Dateninfrastrukturen müssen die Anforderungen der jeweiligen Branche und Datenhoheit, Dezentralität versus Multi-Cloud und Edge-Support sowie Servicebereitstellung berücksichtigt werden. Daher wird z. B. für die Lebensmittelproduktion im Sinne von Industrie 4.0 mit Agri-Gaia ein KI-Ökosystem für die mittelstandsgeprägte Agrar- und Ernährungsindustrie auf Basis der Referenzarchitektur von GAIA-X entwickelt, während die Automobilbranche für die Realisierung von Industrie 4.0 in der Produktion andere Anforderungen für eine Dateninfrastruktur auf der Basis von Gaia-X hat.
Welches sind die wichtigen Faktoren für die zweite Halbzeit bei Industrie 4.0 in den nächsten zehn Jahren?
Wir dürfen in der Forschung und bei der Innovation für die nächste Phase dieser vierten industriellen Revolution nicht nachlassen und weiterhin besonders in die industrielle KI als zweite Welle der Digitalisierung investieren. Die enormen Potenziale von Industrie 4.0 sind noch lange nicht ausgereizt. Dabei spielt die Interoperabilität in Bezug auf die Software- und Hardwarekomponenten eine entscheidende Rolle, gerade auch für den Marktzugang für den Mittelstand und Start-ups. Standards, Normen und Zertifikate sind wichtige Treiber für interoperable Lösungen. Hier müssen wir in Deutschland eine Vorreiterrolle übernehmen, die auch die Resilienz und Sicherheit der angebotenen Lösungen im Fokus hat.
Digitale Souveränität und Resilienz
Letztlich müssen wir die richtige Balance zwischen einer höheren digitalen Souveränität auf der einen Seite, aber auch vertrauenswürdigen und resilienten Lösungen für globale Märkte als führender Industrieausstatter auf der anderen Seite anstreben.
Nach den Erfahrungen in der Pandemie müssen wir Lösungen erarbeiten, um Risse in Lieferketten oder den Produktionsstopp durch kurzfristige Personalengpässe zu vermeiden. Hier können „Homeoffice“-Technologien kaum helfen, sondern es werden „Home Workbenches“ benötigt, welche die mobile Steuerung, Wartung und Reparatur von Fabrikanlagen als Softwarelösungen mit Fernzugriff auf cyber-physische Systeme bis hin zur Teleoperation mit physischen Avataren ermöglichen.
Für die zweite Halbzeit brauchen wir neben diesen technologischen Innovationen aber weiterhin die Unterstützung der Politik und der Gewerkschaften: für die Zukunft der Wertschöpfung ist auch in der nächsten Legislaturperiode weiterhin die erfolgreiche Kooperation auf der Ebene von Plattformen dringend notwendig, um dauerhaft die wirtschaftlichen und gesellschaftlichen Früchte der von Deutschland ausgegangenen vierten industriellen Revolution in deren zweiter Halbzeit ernten zu können.
Weitere Hintergründe zu zehn Jahren Industrie 4.0 lesen Sie in der kommenden Ausgabe Nr. 14 von VDI nachrichten, als E-Paper oder im Zeitungsformat.