Her mit den Akkus
Am Ende ihres Lebenszyklus werden Lithium-Ionen-Akkus zum Entsorgungsproblem. Die Bremerhavener Redux GmbH will es mit einer bislang einzigartigen Anlage im großen Stil lösen.

Foto: Saubermacher
Die Schredderanlage im linken Teil der gut 50 m langen Halle kann noch nicht viele Betriebsstunden absolviert haben. Zumindest sind kaum Kratzer in der gelben Transportschaufel zu sehen, die bis zu 5 t zerkleinerte Altbatterien pro Stunde in die benachbarte Aufbereitungsanlage befördern kann. Auch die Big Packs an der haushohen Sortiermaschine im rechten Hallenflügel sehen neu aus. In aller Ruhe können hier zwei Arbeiter mit einem Gabelstapler das Wechseln der grauen Säcke üben.
Zusammensetzung Lithium-Ionen-Batterie (in %): Gehäuse 15,8, Elektrolyt 11,6, Aktivmasse Kathode 31,5, Ableiter Kathode 6,2, Aktivmasse Anode 18,0, Ableiter Anode 10,6, Separator 6,2
Entwicklung Abfallmengen/Jahr Akkus für E-Bikes und E-Mobile in der EU (in t): 2020: 5000, 2025: 35 000, 2030: 120 000, Recyclingkosten: 1500 €/t bis 2500 €/theu
Quelle: Astrid Arnberger/Saubermacher AG
Zwischen beiden Flügeln steht ein dreigeschossiger Reaktor. Für Besucher oder gar Unbefugte ist er kaum zu sehen, denn er liegt hinter einer hellgrauen Wand verborgen. Das Geheimnis, das um die 40 t schwere Maschine gemacht wird, ist jedoch genauso erklärbar wie die strahlenden Gesichter der Verantwortlichen rundherum.
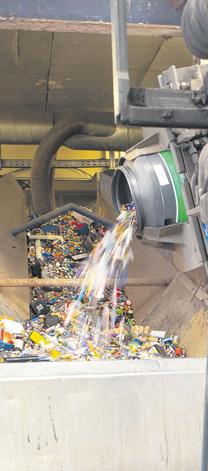
Mit der Anlage will die Redux GmbH – mit einem Jahresdurchsatz von 25 000 t Europas größter Batterierecycler – in Bremerhaven ein neues Kapitel aufschlagen: Künftig werden hier pro Jahr bis zu 10 000 t Lithium-Ionen-Akkus zerlegt. „Wir gewinnen 60 % bis 70 % der Sekundärrohstoffe und des Aktivmaterials zurück und liegen damit weit über der Quote anderer Methoden“, sagt Gerhard Ziehenberger, Technikvorstand der österreichischen Muttergesellschaft Saubermacher AG.
Sechs Jahre für die Entwicklung und zwei Jahre für den Bau sowie Ausgaben von 3 Mio. € liegen hinter Redux und Saubermacher. „Es war und ist ein schwieriger Prozess“, sagt Astrid Arnberger über das Recyclingverfahren und seine Entstehung. Die Wissenschaftlerin und Umweltingenieurin aus der Steiermark hat die Anlage gemeinsam mit den Redux-Experten entwickelt.
Dass der Umgang mit ausgemusterten Lithiumakkus problematisch ist, weiß Redux-Geschäftsführer Holger Kuhlmann aus eigener Erfahrung: Vor sechs Jahren hat der explodierende Stromspender eines E-Bikes ein Großfeuer in seinem Betrieb verursacht. Vielleicht ist dieses Gefahrenpotenzial der Grund, warum andere Recycler die verbrauchten Kraftpakete nicht zerlegen, sondern nur einfach im Hochofen einschmelzen.
Litihium-Ionen-Akkus sind in der Batteriewiederverwendung das Thema der Zukunft. Smartphones, Laptops, Digitalkameras und andere auf elektrische Energie angewiesene transportable Anwendungen sowie die mittlerweile allgegenwärtigen E-Bikes wären ohne die handlichen Kraftquellen nicht denkbar.
Während die Menge der neu eingesetzten Akkus jährlich im zweistelligen Prozentbereich wächst, steigt der Rücklauf an alten Batterien vergleichsweise langsam – sie halten einfach länger als herkömmliche Batterien. „Wir rechnen in den nächsten Jahren mit 2000 t bis 3000 t Altbatterien jährlich“, meint Saubermacher-Vorstandssprecher Ralf Mittermayr.
Doch wenn sich die politischen Ziele in Sachen Elektromobilität verwirklichen, wird schon bald ein gewaltiger Strom verbrauchter Akkus auf die Abfallwirtschaft zufließen. „Europaweit könnten es in zwölf Jahren rund 120 000 t Altakkus pro Jahr sein“, hat Astrid Arnberger errechnet, die an der österreichischen Montan-Universität Leoben ihre Dissertation über die Wiederverwertbarkeit von Lithium-Ionen-Akkus geschrieben hat. Der größte Teil wird aus Elektromobilen stammen.
Wie für alle anderen Batterien und Akkus hat der Gesetzgeber auch für die Lithium-Ionen-Variante eine Rückgabe- und Rücknahmepflicht vorgeschrieben. Die 25 kg bis 595 kg schweren Energiespeichersysteme von Elektromobilen bestehen aus im Schnitt 1,2 M-% (Massenanteile) Kupfer, 3,5 M-% Stahl und 3,6 M-% Aluminium (s. Kasten).
Besonders interessant für die Wiederverwertung sind die Aktivmassen der Kathode (31,5 % der Batteriemasse) und der Anode (18 %), denn sie enthalten unter anderem die seltenen Elemente Kobalt, Mangan, Nickel und Lithium. „Eine Tonne Kobalt kostet derzeit rund 70 000 €“, sagt Ziehenberger. Doch ohne weiteres ist an die wertvollen Materialien nicht heranzukommen. „Ein ausrangierter E-Mobilakku enthält immer noch 80 % seiner Kapazität und die Spannung beträgt bis zu 700 V“, beschreibt Astrid Arnberger die Problematik.
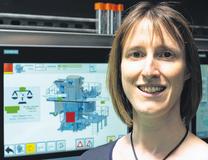
Die Speicher müssen also komplett entladen sein, bevor das Recyling greift. Teilweise geschieht das in der Redux-Zentrale im hessischen Offenbach. Dort wird sogar die Energie wiederverwertet. „Wir speisen den Strom ins Netz ein“, erläutert Arnberger. Anschließend werden die Batterien von ihrem Gehäuse befreit. Geschäftsführer Kuhlmann sagt dazu: „Das ist nur in Handarbeit zu leisten, denn jeder Autohersteller hat praktisch für jedes Modell ein anders geformtes System.“
Praktisch alle Hersteller dürften bereits an seine Tür geklopft haben, weil das bloße Einschmelzen der anderen Recycler kaum dem von der Autoindustrie gewünschten grünen Image entspricht. Dem Vernehmen nach interessiert sich auch Tesla für das Unternehmen, um hier die Altakkus seiner in Europa verkauften Fahrzeuge zu entsorgen. Redux und Saubermacher lassen das unkommentiert. „Ich habe Dutzende von Verschwiegenheitserklärungen unterschrieben“, sagt Kuhlmann. Selbst die von einigen Unternehmen angelieferten Akkus dürfen Betriebsfremde nicht sehen, weil die Stromspeicher ohne Hülle in Bremerhaven eintreffen und die Konstruktion offen sichtbar wäre.
Doch nicht nur um ihre Kunden, auch um die Funktionsweise der Recyclinganlage machen die Bremerhavener ein Geheimnis. Astrid Arnberger beschreibt den vollautomatischen Prozess immerhin in groben Zügen. „Erst werden die entladenen und trockengelegten Teile weiter manuell zerkleinert und sortiert“, erläutert die Umweltingenieurin, „dann werden sie thermisch behandelt, um den Elektrolyt zu verdampfen, und schließlich wird die Masse mechanisch zerkleinert und maschinell in die wesentlichen Stoffgruppen sortiert.“
Das klingt einfach, aber schon bei der Frage nach der Temperatur der thermischen Behandlung werden Österreicher und Bremerhavener gleichermaßen schweigsam. „Die Temperatur liegt unter dem Schmelzpunkt von Aluminium“, mehr lässt sich Arnberger nicht entlocken. Der liegt bei 660 °C.
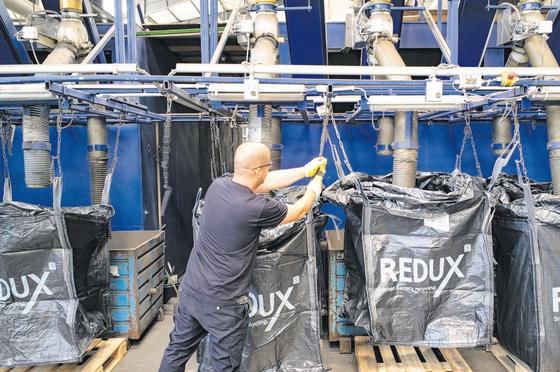
Dass die Entwicklung sechs Jahre dauerte, lässt die Komplexität des Verfahrens erahnen. Die Anlage gilt als Quantensprung in Richtung vollständiger Verwertung. Beim bislang üblichen Einschmelzen entsteht ein nur bedingt verwendbares Endprodukt. Doch auf dem Recyclingmarkt der Zukunft hat derjenige die Nase vorn, der möglichst sortenreine Materialfraktionen liefert, die dann in die Akkuproduktion zurückgeführt werden können.
Die „Saubermacher“ sind deshalb stolz auf ihre Quoten. „3 % Eisen, 25 % Aluminium, 15 % Kupfer und 60 % Aktivmaterial“ des in den Akkus enthaltenen Materials werde am Ende im praktisch reinen Zustand zurückgewonnen, verkündet ein Plakat an der Wand. Auch die restliche Mischfraktion ist noch verwertbar.
Das sortenreine Material kann unmittelbar in die Weiterverarbeitung an Spezialbetriebe gegeben werden, die Kobalt, Mangan und Nickel extrahieren. Diese Reinheit „kann kein anderer“, sagt Produktionsleiter Claas Reckelberg stolz. Und lässt zumindest ein bisschen von dem Prozess in dem drei Stockwerke hohen Reaktor durchblicken.
Nach und nach werden die Bestandteile in gröbere und feinere Fraktionen zerlegt. Mittels Wärme wird die Aktivmasse von der Folie getrennt, auf der sie aufgebracht ist, und zum Ende des Prozesses auf eine Größe von wenigen µm geschrumpft.
Eine Herausforderung bei der Entwicklung der Maschine bestand dabei offenbar in dieser geringen Partikelgröße. So musste verhindert werden, dass die Oberflächen der Maschine verkleben und dass die Partikel durch die kleinsten Spalten nach außen gelangen. Wie die Redux-Experten dieses Probleme gelöst haben, geben sie nicht preis. „Die gesamte Anlage arbeitet staubfrei, sodass hier niemand eine persönliche Schutzausrüstung benötigt“, versichert Ziehenberger.
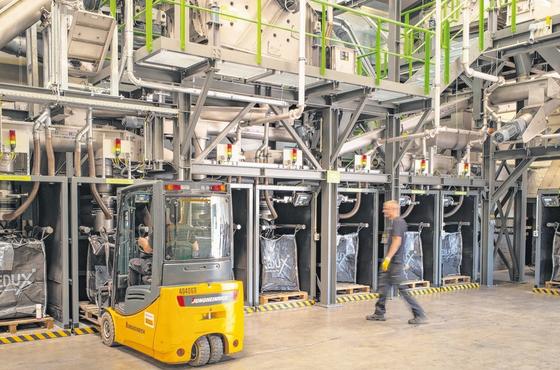
Ausgefeilte technische Lösungen zu entwickeln, steckt gewissermaßen in der DNA des Bremerhavener Unternehmens. Seine Wurzeln reichen bis in die 1990er-Jahre zurück. Als sich am politischen Horizont die deutsche Batterieverordnung abzeichnete, experimentierten ein paar Ingenieure mithilfe der kommunalen Wirtschaftsförderung an Recyclingmöglichkeiten.
1998 trat das Verbot von quecksilberhaltigen Batterien und die Rücknahmeverpflichtung für Hersteller und Handel in Kraft – parallel dazu ging das Vorläuferunternehmen der heutigen Redux GmbH an den Start. Aus der Zeit stammt ein besonderes Röntgengerät als wichtigste Maschine in der Halle gleich neben der neuen Lithium-Ionen-Anlage.
Im Höchsttempo rauschen klassische Haushaltsbatterien jedes Typs durch ein System schmaler Röhrchen. Pro Sekunde werden darin 40 Batterien von Röntgenblitzen durchleuchtet und sofort per Druckluft in den richtigen Sammelbehälter gepustet. „Das System erkennt anhand der Grauschattierungen auf den Röntgenbildern die Art der Batterien“, erläutert Kuhlmann und ergänzt stolz: „20 Jahre alt und und immer noch weltweit Stand der Technik. Nicht schlecht – oder?“
Mit einem Jahresvolumen von 25 000 t Altbatterien ist Redux Marktführer auf dem Kontinent; daran wollen die Bremerhavener und ihre Muttergesellschaft mit der neuen Anlage anknüpfen. Sie ist für eine Jahreskapazität von 10 000 t ausgelegt und kann neben Lithium-Ionen-Akkus auch herkömmliche Batterien aufarbeiten. Für den Eigentümer der Saubermacher AG, Hans Roth, sind die Entwicklungskosten von 3 Mio. € eine gut angelegte Investition: „Wir sind für das absehbar steigende Mengenaufkommen weltweit gut gerüstet.“
Das Batterierecycling will das Team um Roth noch weiter verfeinern. Die Aktivmasse, die Redux mit der neuen Maschine zurückgewinnt und zum Extrahieren von Kobalt, Mangan und Nickel an pyro- und hydrometallurgische Unternehmen weiterleitet, hat einen Lithiumgehalt von 2 % bis 3 %. „Leider geht Lithium bei der weiteren Behandlung oft in die Schlacke oder in die Abluft über und ist hierdurch für die weitere Rückgewinnung nicht mehr wirtschaftlich verfügbar“, erläutert Kuhlmann den aktuellen Stand.
Noch vor der endgültigen Inbetriebnahme haben Deutsche und Österreicher das nächste Forschungsprojekt gestartet. Nun suchen sie nach wirtschaftlichen Wegen, künftig auch Lithium zurückzugewinnen.
Obwohl die weltweiten natürlichen Lithiumvorräte noch mindestens bis zum Jahr 2050 reichen, ist die Rückgewinnung aus alten Akkus ökonomisch interessant: Angesichts der rasant wachsenden Nachfrage für die Elektromobilität hat sich der Preis pro Tonne Lithiumcarbonat innerhalb eines Jahres auf 14 500 $ mehr als verdoppelt.