So gelingt der 3-D-Druck mit Metall
Ein Aachener Jungunternehmen hilft seinen Kunden, optimale Parameter für das selektive Laserschweißen zu finden.

Foto: Aconity3D
Eigentlich kann gar nichts schief gehen beim pulverbettbasierten 3-D-Druck. Die Theorie ist jedenfalls denkbar einfach: Ein Laser schmilzt Metallpartikel Schicht für Schicht zum Bauteil zusammen. Fertig!
Bei der additiven Fertigung von großvolumigen Kunststoffteilen spielt die Qualitätskontrolle bisher oft nur eine Nebenrolle. Denn Blumenvasen, Werbefiguren oder Möbelstücke funktionieren auch dann, wenn Soll- und Ist-Werte minimal voneinander abweichen.
Wer aber Teile für die automobile Serienproduktion zuliefern will, hat Genauigkeit zu garantieren. „Um industriefähig zu sein, muss man zu jedem Produkt nachverfolgbar darlegen können, unter welchen Bedingungen es wann und wo entstanden ist“, sagt Stephan Beyer, CEO der BigRep GmbH. „Ein einfaches Condition Monitoring beim Drucker, also etwa die Temperaturkontrolle, reicht nicht aus.“ Die Berliner stellen XXL-Drucker für professionelle Anwendungen her.
Um eine lückenlose Dokumentation gewährleisten zu können, arbeitet BigRep nun mit Bosch Rexroth zusammen. Im Rahmen der Entwicklungspartnerschaft werden künftige Drucker mit CNC-Steuerungs- und Antriebssystemen ausgerüstet. „Dann lässt sich jede einzelne Schicht minutiös protokollieren“, so Beyer. „Die Rexroth-Komponenten sind außerdem ausgezeichnete Schnittstellen, um unsere 3-D-Drucker mit voller Konnektivität in bestehende Produktions- und Automationssysteme zu integrieren.“ Dies werde den 3-D-Druck als Schlüsselelement für Industrie-4.0-Anwendungen verankern. sta
Die Praxis ist aber ungleich komplexer. Denn die Qualität des Endprodukts ist von sehr vielen Einflussfaktoren abhängig. Sie kann sich sogar schon dann verändern, wenn lediglich ein anderer Pulverlieferant gewählt wird oder sich Strömungsbedingungen der Rauchgasabsaugung während des Produktionsprozesses ändern. Kritiker der additiven Fertigung behaupten deshalb: Kein Teil gleiche dem anderen. Drum tauge das Verfahren weder für die Großserienfertigung noch zur Herstellung sicherheitsrelevanter Bauteile.
Yves Hagedorn, Geschäftsführer der Aconity3D GmbH aus Herzogenrath, ist anderer Meinung. Er hilft seinen Kunden dabei, die optimalen Prozessparameter für alle erdenklichen Materialien und Anwendungsbereiche zu finden.
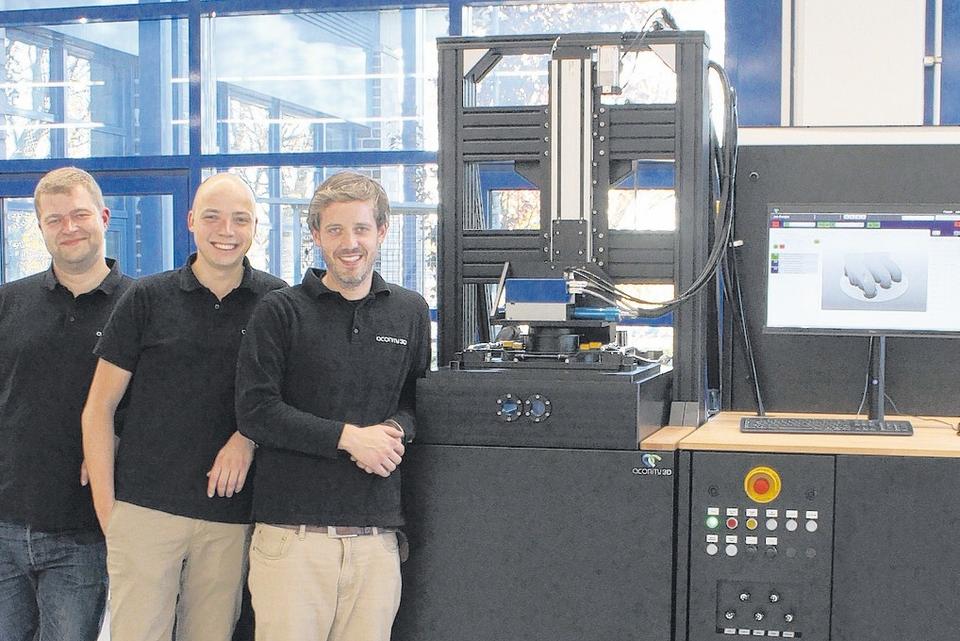
Möglich macht das die besondere Architektur der Aconity-Maschinen: „An unseren Druckern lassen sich beispielsweise Laserleistung, Pulsfrequenz und -dauer ebenso anpassen wie die Scanvektorlänge, der Scanvektorversatz und die Pulverschichtdicke“, so der 35-Jährige. Mit anderen Worten: Das Team bietet seinen Kunden ein riesiges Experimentierfeld. Das hat schon viele namhafte Vertreter aus Wissenschaft und Wirtschaft überzeugt – etwa das MIT, Toyota und Siemens.
Ein großes Experimentierfeld alleine würde aber keine nachhaltige Freude machen, wenn sich der Druckprozess nach Anpassung einzelner Parameter nicht in Echtzeit und bis ins kleinste Detail beobachten ließe. Deshalb beherrschen die Aconity-Maschinen gleich zwei In-Situ-Prüfverfahren: Ein Highspeedmonitoring und die Pyrometrie.
Das Highspeedmonitoring basiert auf einer Hochgeschwindigkeits-CMOS-Kamera. Sie blickt koaxial durch den Scanner auf das Pulverbett. „Bei einer ausreichend starken Beleuchtung kann man dann – trotz des hellen Laserstrahls – die Dynamik im Pulverbett verfolgen“, so Hagedorn. „Man sieht beispielsweise, wie das Gros der Partikel in das Schmelzbad hineinfließt, während ein kleiner Teil aufgrund der Thermik weggeblasen wird.“ Deutlich erkennbar sei außerdem, wie sich die Schmelzbadgröße in Abhängigkeit der Verfahrensparameter – etwa Laserfrequenz und der Pulsdauer – verändert. „So bekommt man sehr schnell ein Gespür dafür, welche Parameter in festen und dichten Teilen münden“, so Hagedorn. „Zur rückgekoppelten Steuerung werden die Filme aber noch nicht benutzt.“ Es fehle an geeigneten Algorithmen zur Echtzeitauswertung der großen Datenmengen, um Rückschlüsse auf die optimale Parametrierung ziehen zu können.
Anders verhält es sich bei der pyrometrischen Analyse. Sie kann genutzt werden, um aktiv in den Prozess einzugreifen. Das Verfahren wertet statt des sichtbaren Lichts nur die Infrarotstrahlung aus. Analysiert wird dabei ein Fleck, der ungefähr so groß ist wie der Laserspot – störende Umgebungseinflüsse bleiben also außen vor. Die Messgeschwindigkeit ist mit 100 kHZ sehr hoch.
Die gemessene Strahlungsintensität ist immer abhängig von der Scangeschwindigkeit und der Vektorlänge. Anders ausgedrückt: Je schneller der Laser wieder in der Nähe eines zuvor aufgeschmolzenen Punktes ist, desto größer ist die thermische Emission.
Eine hohe Emissivität deutet auf eine große Wärmeeinflusszone im Material hin. Das wiederum geht einher mit einem großen Schmelzbad. Problematisch daran: Unter großen Schmelzbädern leidet die Geometriegenauigkeit. „Pfützen haben niemals scharfe Ecken“, erklärt Hagedorn anschaulich.
Außerdem kann es bei einer entsprechend suboptimalen Parametrierung zu lokalen Verdampfungen und damit zu Gasporen im Bauteil kommen. Ist hingegen der Energieeintrag zu klein, sind Fehlstellen und Lunker möglich. Schlimmstenfalls können sich Schichten aufgrund einer fehlenden Anbindung auch voneinander lösen, dann wölben und letztlich die Abstreifer zum Pulverauftrag beschädigen.
Die Schmelzbadgröße hat außerdem Einfluss auf die Mikrostruktur: Große „Pfützen“ kühlen langsamer ab als kleine. Dadurch entstehen große Korngrenzen – also Schwachstellen im Gefüge.
„Die Kunst ist nun, für jedes Material genau die Emissivität zu identifizieren, die in optimalen Bauteileigenschaften münden“, sagt Hagedorn. „Gesucht wird also der goldene Pfad. Darauf vereinen sich Laserleistung, -pfad und -pulsfrequenz sowie Pulverschichtdicke zu einem Optimum.“ Das setze Parameterstudien voraus. Daran arbeitet Aconity3D in Kooperation mit Kunden.
Die Vision: Sind die optimalen Einstellungen für neue Materialien einmal festgelegt, kann sich der Drucker dank der permanent registrierten Emissionswerte automatisch darauf einstellen. Ergebnis sind optimale Bauteile – zu jeder Zeit, unter allen Bedingungen.