„Um die breite Kundschaft zu überzeugen, ist Carbon noch zu teuer“
Der Erfolg der Elektromobilität hängt entscheidend davon ab, welche Fortschritte die Materialforschung im Bereich Hochvoltbatterien und Leichtbau macht. U.a. als Forschungsleiter der SGL Group kämpft Dr. Hubert Jäger in beiden Feldern an vorderster Front. Im Interview erläutert er wirtschaftliche Perspektiven und technische Herausforderungen der Zukunftstechnologien.
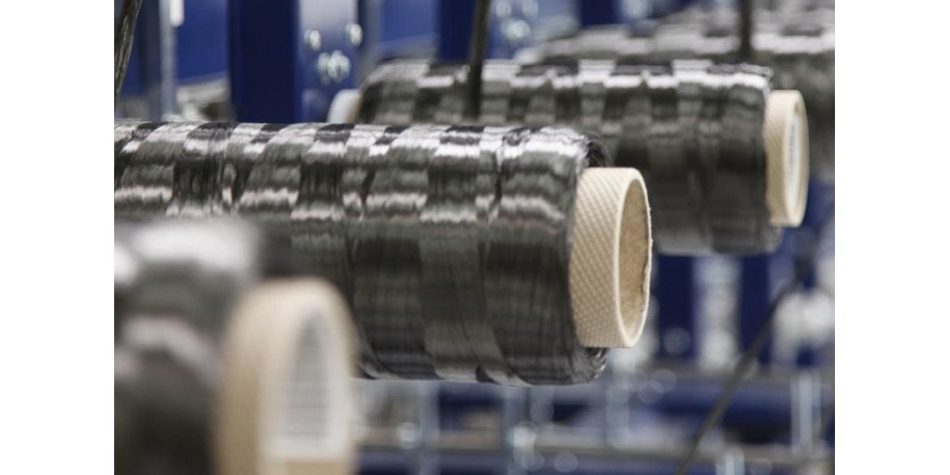
Foto: BMW
VDI nachrichten: Als Vorstandsvorsitzender im „Kompetenznetzwerks Lithium-Ionen-Batterien (KliB)“ haben Sie die deutsche Batterieforschung im Blick. Wie bewerten Sie die Fortschritte?
Jäger: Die Batterieforschung musste buchstäblich wiederbelebt werden. Heute gibt es wieder rund 1000 Forscherinnen und Forscher, die vor allem in den drei Zentren Ulm, Münster und Karlsruhe sowie in Dresden und Braunschweig arbeiten. Damit ist eine Grundvoraussetzung geschaffen, um zur Spitze aufzuschließen. Das ist uns in den letzten fünf Jahren gelungen.
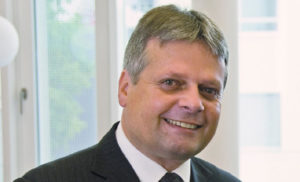
Der studierte Chemiker ist Forschungsleiter der SGL Carbon und steht dem dem Forschungsverbund Carbon Composites e.V. (CCeV) vor.
Auch an der Spitze des Industrieverbundes Kompetenznetzwerk Lithium-Ionen-Batterien (KLiB) macht er sich für E-Mobilität stark.
Sie sehen die deutsche Batterieforschung also schon auf dem Niveau von Japan, Korea und den USA?
Ja. Wir haben viel verlorenes Terrain zurückgewonnen, obgleich die Produktion noch nicht wieder in Deutschland angekommen ist. Das ist ein Nachteil im Wettbewerb.
Inwiefern ein Nachteil?
Es fehlt die Fertigungstechnik und Automation. In der Forschung haben wir das Zeug, eine Führungsrolle einzunehmen. Und wir haben die gesamte Prozesskette im Land, die wir nun in Forschungsfabriken Stück für Stück zusammenführen müssen. Denn noch fehlt die Zellfertigung. Der Fokus muss ganz klar auf der Produktionstechnik und der Kostensenkung durch Automatisierung liegen. Das gehen wir an.
Wie?
In Ulm bauen wir mit Fördermitteln von Bund und Land eine Forschungsfabrik für über 30 Mio. € auf. Dort lassen sich bis zu 100 000 große Batteriezellen pro Jahr fertigen. Die Produktionslinie ist modular aufgebaut, damit technischer Fortschritt in einzelnen Prozessen durch Austausch der Module umgehend Eingang findet. In das Projekt sind Rohstofflieferanten, Hersteller von Fertigungstechnik, Spezialisten für Automatisierung und weitere Nutzer involviert, die hier gemeinsam den Schritt zur nächsten Generation von Lithium-Ionen-Batterien gehen wollen.
Die Hoffnungen ruhen auf der nächsten Batteriegeneration?
Bei der jetzigen werden wir den Vorsprung der internationalen Wettbewerber nicht aufholen. Aber für die nächste Generation, die etwa 2025 zu erwarten ist, sehe ich sehr gute Chancen. Mit der jetzt aufgebauten Kompetenz kann es uns gelingen, die Produktion nach Deutschland zurückzuholen.
Als Forschungsleiter von SGL sind Sie über das Anodenmaterial Graphit direkt in die Forschung involviert. Bleibt Graphit der Werkstoff der Wahl?
SGL hat über die Kooperation mit japanischen Consumer-Batterieherstellern in den letzten 15 Jahren viel Kompetenz auf diesem Gebiet aufgebaut. Wir sind weltweit einer der größten Hersteller des Anodenmaterials Graphit. In der nächsten Generation wird dem Anodengraphit Silizium beigemischt, um die Speicherkapazität zu erhöhen. Etwa 2020 sind erste Prototypen auf dieser Basis zu erwarten.
Wo liegt die Herausforderung?
Wir müssen eine wirklich homogene Verteilung der Graphit- und Siliziumanteile im sogenannten Slurry – also der Anodenpaste – hinbekommen. Das Material muss auf Nanomaßstab gemahlen, angerührt und mit Abweichungen von maximal 1 µm bis 2 µm auf hauchdünne Folien ausgebracht, gewalzt und getrocknet werden. Da haben wir sowohl auf Materialseite als auch auf Produktionsseite noch eine Menge zu tun. Aber wir arbeiten schon heute an der Technik für 2025 – und sind auf einem guten Weg.
Nun kündigt Tesla gerade eine vier bis fünf Mrd. $ schwere Investition in eine riesige Batteriefabrik an. Bedroht das die deutschen Pläne?
Sie bauen dort Großzellen, die sie einzeln verkabeln. Das weicht von europäischen und japanischen Konzepten ab, sollten wir aber beileibe nicht auf die leichte Schulter nehmen. Tesla will bis 2020 rund 500 000 Autos bauen. Das käme der Verdoppelung des heutigen Weltmarkts für Lithium-Ionen-Speicher gleich. Ich sehe in dem Konzept eine Gefahr, dass es die Forschung und Entwicklung entschleunigt. Denn Tesla kann es gelingen, heutige Technik durch Skaleneffekte auf marktfähige Kosten zu bringen und die Qualität zu stabilisieren.
Keine guten Nachrichten für die Europäer also?
Doch! Für die Elektromobilität und den Batteriemarkt ist das ein toller Impuls, über den wir uns alle freuen. Wir werden uns in der Forschung für die nächste Generation aber nicht beirren lassen. Ich bin weiterhin überzeugt, dass die entscheidenden Impulse im Batteriemarkt künftig aus Europa kommen werden.
Als Vorstandsvorsitzender des „Carbon Composites e.V.“ engagieren Sie sich auch sehr für den CFK-Standort Deutschland…
…da mir beide Themen am Herzen liegen und der Leichtbau mit der Elektromobilität ganz direkt in Zusammenhang steht. Beim Auto ist Abspecken leichter als beim Fahrer – mit einer Diät sind 300 kg Zusatzgewicht einer Batterie nicht zu kompensieren. Mehrgewicht schlägt aber direkt auf die Reichweite. Als Faustformel gilt: 2 kg Batteriemasse bringen heute 1 km Reichweite. Das muss an anderer Stelle kompensiert werden. Elektromobilität braucht also Leichtbau.
Stromer wie der BMW i3 oder VWs 1-Liter-Auto XL1 sind erste Meilensteine. Doch der Weg in die Großserie ist teuer und lang. Wie sehen Sie die Perspektiven?
Leichtbau mit Carbon ist noch zu teuer. Doch die Fasern kommen aus der Raumfahrt, sind heute in der Luftfahrt etabliert und kommen dem Automobilmarkt näher. Noch sind wir hier in den Kinderschuhen, aber es geht voran.
Was macht Sie da so sicher?
BMW hat vorgemacht, wie es gehen kann. Sie haben aus sonst 350 Karosserieteilen 35 Teile aus Carbon gemacht. Je weniger Teile, desto günstiger die Fertigung. Das reicht noch nicht. Denn wir als Kunden bestimmen über unsere Zahlungsbereitschaft, welche Technik in den Markt kommt. Um die breite Kundschaft zu überzeugen, ist Carbon noch zu teuer.
Wie kommen die Preise runter?
Heute liegen die mittleren Kosten im Carbon-Leichtbau bei 100 €/kg. Davon 20 € Material und 80 € Fertigungskosten. Das Ziel ist es, die Fertigungskosten um 90 % zu senken. Und das ist realistisch. Dann wären wir bei 30 €/kg. Immer noch teurer als Stahl oder als Aluminium. Aber dann zahlen sich anderen Vorteile aus: Funktionsintegration durch bessere Formbarkeit, weniger Teile, Wegfall der energieintensiven KTL-Tauchbäder vor dem Lackieren, etc.
Wie ist die Kostenreduktion um 90 % zu schaffen?
Wir haben in Dresden, München, Kaiserslautern, Aachen, Stuttgart – um nur einige zu nennen – herausragende Forschungsinstitute. Diese Institute sind über unseren Verein im Dialog und stimmen sich ab, in welche Richtung sie forschen und entwickeln. Wir können als Industrie direkt auf ihren Forschungsergebnissen aufsetzen und innovative Prozesse und Verfahren daraus ableiten. Dabei hilft uns auch der Spitzencluster MAI Carbon. Unser Weg hat nur eine Richtung: Automatisieren, Automatisieren und noch einmal Automatisieren. Wir sind überzeugt, dass wir mehr als 90 % schaffen. In den Instituten sind die Grundlagen dafür gelegt.
Welche Rolle spielen die Materialien?
Eine eminent wichtige! Thermoplaste erlauben kurze Zyklenzeiten. Doch dafür muss die Anbindung der Fasern an die Harzmatrix optimal sein. Bei SGL haben wir jüngst eine Carbonfaser mit einer neuen Schlichte entwickelt, die hier große Verbesserungen verspricht.
Schlichte?
Die Kohlenstofffaser wird in einem Tauchprozess minimal mit einer Polymerlösung beschichtet. Diesen Film nennen wir Schlichte. Sie verbessert die Haftung zwischen Harz und Faser. Dafür muss sie chemisch und thermisch stabil sein.
O.K. Zurück zu den Thermoplasten…
…die nicht nur schnelle Produktionszyklen erlauben, sondern auch Umformbarkeit und die Frage des Recyclings entscheidend verbessern. Mit unserer neuen Faser gehen wir jetzt auch direkt in die MAI-Carbon-Projekte zur Bauteilfertigung. Eine der ganz großen Fragen, die es für die Serienfertigung im Automobil zu beantworten gilt, ist die Frage, wo im Fahrzeug der Einsatz von Carbon Sinn macht und welcher Fasertyp für welche Bauteile geeignet ist. Heute stehen 1,4 Mrd. t Stahl, 65 Mio. t Aluminium und 40 000 t Carbonfasern gegenüber. Schon aus diesen Zahlen wird klar: Leichtbau wird im Materialmix umgesetzt. Das richtige Material muss an den richtigen Ort – wobei die Bauteilbelastung entscheidet. Zum Thema Hybridbauweise entstehen gerade in Dresden und Wolfsburg Leuchtturmprojekte.
Auch Energie- und Ökobilanzen werden in der Automobilindustrie wichtiger. Welche Rolle können pflanzlich basierte Fasern spielen?
Sie können alles in Kohlenstoff überführen. Aber für industrielle Einsätze brauchen sie ein verlässliches Eigenschaftsprofil – also definierte Festigkeit und Steifigkeit. Lignin als Fasermaterial hat sehr viele Fehlstellen, an denen Risse und Aufspaltungen vorprogrammiert sind. Naturfasern haben bisher nicht die benötigten Eigenschaften. Und auch die vermeintlichen Kostenvorteile haben sich in jüngeren Forschungen sehr relativiert. Ich bin überzeugt, dass es in Zukunft einen Markt für pflanzliche Fasern geben wird. Aber die Einsatzgebiete werden begrenzt sein.
Doch es gibt Zweifel an den energetischen Vorteilen von Carbon gegenüber Stahl und Aluminium in Well-to-wheel-Betrachtungen. Was antworten Sie Zweiflern?
Die kontroverse Diskussion ist nötig und wird uns erhalten bleiben. Alle Vergleiche hinken. Weder sind Aluminiumautos ein Verbrechen an der Umwelt, noch ist CFK zu energieintensiv oder Stahl stets billig. Hoch- und höchstfeste Stähle sind etwas ganz anderes, als Recyclingstähle. Auch bei Aluminium sind Legierungen im Einsatz, die den Einsatz von Recyclingaluminium begrenzen.
Wo liegt dann der Denkfehler?
Die Bilanzen müssen die gesamten Materialsysteme betrachten, um sinnvolle Vergleiche anstellen zu können. Es wird noch dauern, bis wir so fundierte Bilanzen bekommen. Letztlich werden die Automobilhersteller Treiber dafür sein, weil sie verlässliche Vergleiche zwischen den Werkstoffen brauchen.
Eine letzte Frage zum Leichtbau. SGL verdient viel Geld mit Graphitelektroden für Hochöfen. Wie passt das zu Ihrem Engagement im Carbon-Bereich?
Die beiden Märkte stören sich nicht. Graphitelektroden sind ein Verbrauchsmaterial im Stahlrecycling. Pro t Recyclingstahl braucht es etwa 1 kg Graphit. Wir sind in dem Markt mit jährlich 400 Mio. t Recyclingstahl größter Elektrodenhersteller. In diesem Markt ist von den 40 000 t Carbonfasern weltweit nichts zu spüren.
Wie sehen Sie als Forschungschef die angespannte Lage der SGL Group?
Sie heben auf unser Restrukturierungsprogramm ab. Es ist nicht das erste seiner Art in der Geschichte unseres Unternehmens. So wie wir es anpacken, also Fokussierung auf die Kerngeschäfte und Verjüngung der Altersstruktur, wird es SGL stärken. Die Balance zwischen Sparkurs und Zukunftsinvestitionen ist nach meinem Ermessen gewahrt. Wir werden die Marktpotenziale künftig schneller erschließen.
Wie sehr muss Ihre Forschungsabteilung bluten?
Ich sehe es nicht als Bluten. Aus unserer Abteilung wechseln junge Hoffnungsträger auf die frei werdenden Stellen in den Fachabteilungen. Das stärkt die SGL und dient dem Know-how-Transfer aus der Forschung ins gesamte Unternehmen. Ich muss 10 % bis 15 % meiner Leute in die Organisation abziehen lassen, aber ich glaube, dass sie unser Forschungsnetzwerk stärken und die Innovationskraft unserer Gruppe heben.