Lack vom Fließband
Für jeden Zweck gibt es heute einen besonderen Lack. Die Rezeptur und Prüfung solcher Spezialbeschichtungen erfolgen bei Evonik vollautomatisch. Ein Besuch im Lacklabor.

Foto: Evonik
Leise rieselt das Pulver vom Messlöffel. Knatschrosa ist es und so fein, dass es sich sofort wie Staub auf die wässrige Flüssigkeit legt, die bereits im Becherglas schwimmt. Das farbige Pigment ist extrem wasserabstoßend; es kann sich nicht mit der flüssigen Lösung mischen. Das muss es aber, wenn ein ordentlicher Lack auf Wasserbasis entstehen soll.
Der Essener Konzern für Spezialchemie ist einer der führenden Anbieter von Additiven für wasserbasierte Formulierungen, Hochleistungsadditiven, Vernetzern und Mattierungsmitteln.
Rund 2000 Produkte entwickelt Evonik für die Beschichtungs- und Farbenindustrie. 2016 erzielte das Unternehmen in dem Bereich ca. 2 Mrd. € Umsatz, bei einem Gesamtumsatz von 12,7 Mrd. €.
Forschungs- und Anwendungstechniklabore betreibt der Konzern u. a. in Deutschland, den USA, China, Indien und Singapur. BER
Jetzt kann nur ein Dispergieradditiv helfen. Die Substanz vermittelt zwischen Pigment und Wasser, damit sie sich vermischen. Michael Fiedel, im Geschäftsgebiet Coating Additives von Evonik für die Produktsynthese verantwortlich, holt ein Pulver aus dem Regal und streut eine Messerspitze davon auf die Staubschicht.
Schon fängt es im Becher wild an zu schäumen. Jetzt muss es schnell gehen: Fiedel greift sich rasch ein anderes Fläschchen vom Bord und schüttet ein helles Pulver hinzu. Das Additiv soll Lufteinschlüsse unterbinden. Und tatsächlich: Der Schaum sackt prompt in sich zusammen. „So geht es manchmal munter weiter: Kaum ist das eine Problem behoben, taucht sofort ein neues auf“, beschreibt der Chemiker das mühsame Geschäft der Lackentwicklung.
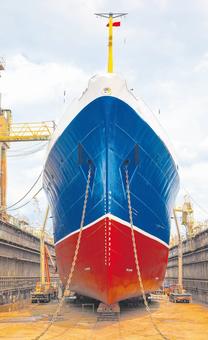
Autos, Häuser, Produktionsanlagen und Konsumgüter soll Lack vor Rost, UV-Licht und Bewuchs schützen oder bestimmte Funktionen übernehmen, z. B. bei Elektronikgeräten die Leitfähigkeit verändern. Zu Europas führenden Lackherstellern gehören Akzo Nobel, BASF, Jotun und Hempel. Allein die deutsche Industrie hat im vergangenen Jahr ca. 1,7 Mio. t Lacke und Farben produziert. Gesamtwert rund 5,4 Mrd. €, beziffert der Verband der deutschen Lack- und Druckfarbenindustrie.
Es ist eine Mischung aus Handwerk, Wissenschaft und Kunst, die Lacke mit ganz speziellen Eigenschaften hervorbringt. Dafür braucht es viele Zutaten: Pigmente, die nicht immer farbig sein müssen, Bindemittel, die dem Lack die Struktur geben, Füllstoffe und Rheologiezusätze für die optimale Viskosität, Entschäumer und Entlüfter für einen blasenfreien Anstrich und Stoffe, die die Haptik beeinflussen. Nur so fühlt sich der Lack hinterher auch „richtig“ an.
Als oberstes Gebot im Labor gilt: die einzelnen Bestandteile exakt nach vorgegebener Rezeptur zusammenbringen. Fachleute sprechen von der Formulierung des Lacks. „Ist der Prozess aber nicht festgelegt, weil es das Produkt noch gar nicht gibt, dann ist das schwierig“, erzählt Fiedel.
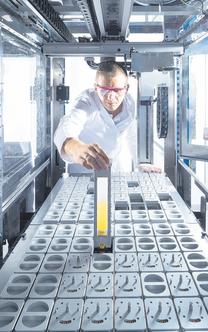
Wie aber findet die Laborcrew das richtige Additiv? Bei nur je zehn Farbpigmenten, Härtern, Bindemitteln und anderen Zusätzen etwa für UV-Schutz ergeben sich schon mal 10 000 Kombinationen. Diese von Hand auszuprobieren, verlangt höchste Präzision und Konzentration.
„Trotz aller Sorgfalt schleichen sich da schon mal Fehler ein“, gesteht der Chemiker. Vor einigen Jahren hat Evonik deshalb den Anlagenbauer Chemspeed aus dem schweizerischen Füllinsdorf nahe Basel ins Boot geholt, um eine vollautomatische Teststrecke für Lacke zu konzipieren.
Die neue Hochdurchsatzanlage, kurz HTE für high throughput experimentation, sei einmalig auf der Welt. „Eine außerordentliche Ingenieursleistung“, meint Claudia Bramlage. Die blonde Chemieingenieurin vom Innovationsmanagement im Geschäftsgebiet Coating Additives ist verantwortlich für den 120 m² großen Raum voller Glas, Kabel, glänzendem Edelstahl und blau lackierten Metallrahmen.
Je nach Prüfauftrag kombiniert sie bestimmte Funktionseinheiten der modular aufgebauten Anlage. Auf Schienen durchlaufen die Lackproben die Stationen, 13 Roboterarme greifen sie sich vom Band, bearbeiten sie und erledigen die oft monotone Arbeit, die früher Laboranten und Chemiker ausführten. Vieles geschieht zeitgleich.
Mit einem leisen Rattern schiebt sich ein neues Gestell an den Startpunkt der Anlage. Von vorne sieht sie aus wie ein schlichter Stahlschrank. Ordentlich aufgereiht steht hier Glas an Glas auf dem Träger und wartet darauf befüllt zu werden. Jeder Behälter ist mit einem Barcode versehen, denn bei Bedarf müssen alle Informationen blitzschnell ausgelesen sein.
Plötzlich ergießt sich mit hauchdünnem Strahl der erste Rohstoff ins Becherglas. Zäh tropft das Bindemittel hinterher. Während das Pigment obendrauf rieselt, staubt es ein wenig. Eine Waage unter dem Träger kontrolliert jede Dosierung automatisch: Das Gewicht stimmt.
Diesen Prozess zu automatisieren, war eine kleine Herausforderung. „Für die Entwicklung der Wägeeinheit brauchte es eine Menge Hirnschmalz der Ingenieure“, erzählt Chemiker Fiedel schmunzelnd. Das Ergebnis: eine Dosierung bis auf wenige Milligramm genau. Von Hand wäre diese Präzision auf Dauer nicht zu erreichen.
Welche Zutaten es jeweils sein sollen, hat das Team zuvor entsprechend der Anforderungen des Kunden programmiert. Auch diese Infos sind im Barcode hinterlegt. Der große Vorteil der automatisierten Prozesse: Jede Formulierung lässt sich reproduzieren, jeder Lack wird sofort appliziert, das Ergebnis beurteilt und anschließend dokumentiert.
Wie von Geisterhand gleitet ein Tablett mit Gläsern über die Schienen zum Homogenisieren. Die einzelnen Bestandteile müssen gut durchmischt sein, sonst ergibt es keine einheitliche Masse. Ein paar Glasperlen plumpsen in jedes Gefäß. Mit Hochgeschwindigkeit wirbeln sie durchs Glas, sobald der Speedmixer startet. Die Murmeln zerreiben die Pigmente und mischen die Zutaten blitzschnell. Und schon ergießt sich der Inhalt eines Bechers gezielt über einen Filter, um die Glasperlen wieder abzutrennen. Fertig ist der Lack!
„Jede einzelne Formulierung zu optimieren ist unser Ziel“, sagt Bramlage. Evonik richtet sich nach den Wünschen der Lackindustrie, entwickelt aber auch Substanzen fürs eigene Geschäftsgebiet Coating Additives. Es ist Teil von Specialty Additives, einem der vier Wachstumskerne des Konzerns, der mit Farben und Beschichtungen 2016 rund 2 Mrd. € Umsatz machte. Im letzten Jahr erwirtschaftete das Essener Unternehmen insgesamt etwa 12,7 Mrd. € mit Spezialchemikalien für Konsum- und Pflegeprodukte, Nahrungs- und Futtermittel, für den Maschinenbau, die Bauwirtschaft und die Elektrotechnik.
Gespannt verfolgt Fiedel in seinem weißen Laborkittel, wie die Probe weiterzuckelt. Denn jetzt kommt die Probe aufs Exempel: Der neue Lack muss gut zu verarbeiten sein und eine gleichmäßige Oberfläche bilden. So viele Additive gibt es, da zeigt erst das Experiment, ob sie ihren Zweck auch erfüllen. Sonst ist die ganze Formulierung Ausschuss.
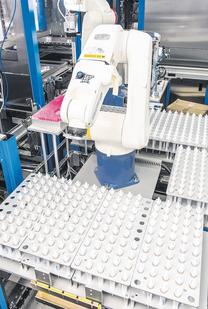
Ein Roboterarm schnappt sich eine frische Kanüle und setzt fünf Tröpfchen Farbe fein säuberlich auf einer Karte ab. Ein Schieberchen mit kleinen Rillen verstreicht den Lack gleichmäßig mit einer festgelegten Schichtdicke. Immer wieder fährt es kurz durch eine Waschstraße, dann zischt eine Druckluftdüse, um es trockenzupusten. Die nächste Probe kann kommen.
Erneut schiebt sich das Gestell hoch, zielsicher greift der Roboter eine Probe, obwohl dort viele Gläschen derselben Farbe stehen. Das System weiß exakt, welche Probe gerade dran ist. Auch wenn sie noch so aufmerksam durch ihre Brille blickt, sie könnte die Menge kaum auseinanderhalten, sagt Anlagenchefin Bramlage: „Wenn wir Bindemittel testen, kann man das von außen nicht wahrnehmen, dann sehen alle Töpfchen irgendwie gleich aus.“
Nebenan appliziert ein Roboterkollege eine Lackprobe im Spritzverfahren. So wenden die meisten Kunden das Produkt später an. Der Roboterarm nimmt die Farbe auf, zischend schießt er sie mit Pressluft auf die Karte. Die meisten Lacke bestehen heute auf Wasserbasis. Trotzdem kann eine Probe auch mal Lösungsmittel enthalten. Weil der Farbnebel zündfähig wäre, saugt ein Dunstabzug permanent die Luft ab.
Evonik testet die Streichfähigkeit und das Trocknungsverhalten der Rezepturen auf Glas, Metall, Edelstahl, Aluminium und Holz – und wenn gewünscht sogar auf den Bauteilen des Kunden. Dann geht es ab in den Ofen. Das beschleunigt die Trocknung. Automatisch fährt ein Gestell mit den Proben hinein und kommt nach definierter Zeit wieder heraus. Fiedel freut sich: Der Lack ist gleichmäßig getrocknet, es haben sich weder Risse noch Krater gebildet.
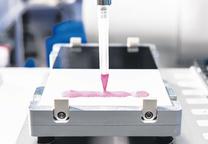
Das Ergebnis der Applikation begutachtet heute kein Mensch mehr. Das übernehmen jetzt Kameras und Sensoren. Der Lack muss sich gut verstreichen oder spritzen lassen, beim Trocknen darf keine Orangenhaut entstehen. Ist die Oberfläche farbecht, fühlt sie sich glatt und angenehm an, gibt es keinen Abrieb, dann stimmt die Qualität.
Denn kleine Unebenheiten auf der frischen Lackschicht haben fatale Folgen. Fremdstoffe könnten sich darin verfangen. Auf dem Anstrich von Ozeanriesen etwa dürfen keine Muscheln anhaften, das macht die Pötte langsamer und führt zu einem höheren Verbrauch an Schiffsdiesel. Werften verwenden deshalb Lacke, bei denen meist Biozide, also toxische Substanzen, den Aufwuchs verhindern.
Die Automobilindustrie legt aus optischen Gründen Wert auf die Lackeigenschaften. Porsche etwa bietet seinen 911er mit einem Effektlack an, der – je nach Blickrichtung des Betrachters – in einer anderen Farbe schimmert. Kostenpunkt: 80 000 € pro Fahrzeug. Rolls-Royce nennt gar nicht erst den Preis seines Lacks, in dem 1000 Diamanten für einen ganz besonderen Glanz sorgen.
Bis zu 120 verschiedene Lackformulierungen testet die HTE-Anlage am Tag. Die Ergebnisse der Qualitätsprüfung fließen in eine Datenbank ein. „Ist der perfekte Lack gefunden, erhalten wir das Rezept auf Knopfdruck“, erzählt Bramlage. Den Kunden wird es mit exakten Dosierangaben zu Pigmenten, Bindemitteln und anderen Additiven geliefert, damit bei der Produktion nichts überschäumt.