Karosseriebau im Vergleich: Was BMW und e.Volution anders machen als Tesla & Co.
Immer mehr Automobilhersteller folgen dem Konzept von Tesla und setzen auf Gigacasting im Karosseriebau. Es geht aber auch anders. Wir stellen die Alternative vor.
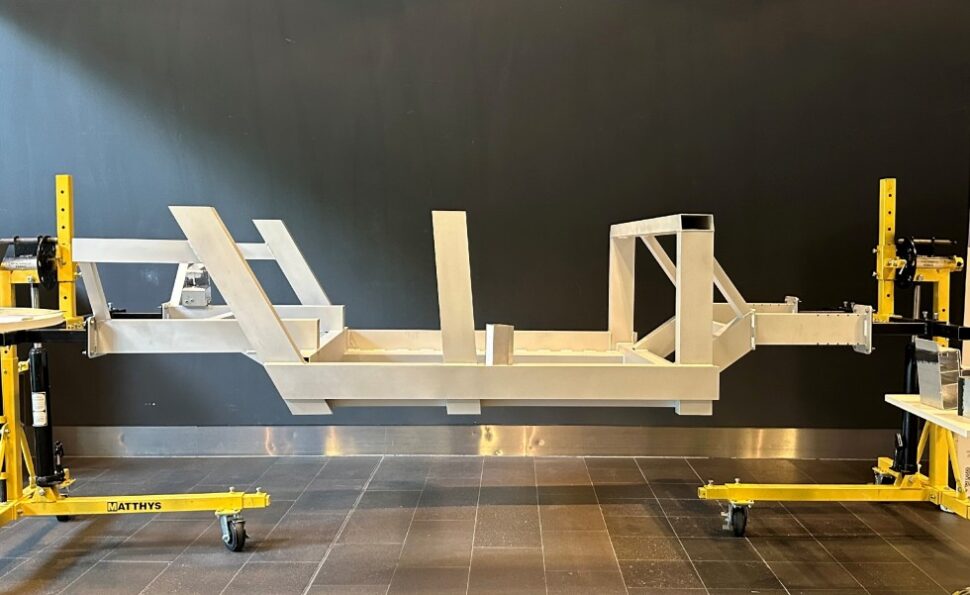
Foto: e.Volution GmbH
Bisher basierten die meisten Elektroautos auf den gleichen Fahrzeugstrukturen wie klassische Verbrenner. Doch das ändert sich gerade. Denn für hohe Reichweiten gilt es möglichst viele Batteriezellen in der Karosserie unterzubringen. So überrascht es nicht, dass Tesla inzwischen auch zu den Vorreitern für neue Produktionskonzepte im Automobilbau gehört. Manche Automobilhersteller scheinen inzwischen auch auf das Tesla-Konzept mit möglichst großen Druckgussteilen aus Aluminium zu setzen. Dagegen setzen andere auf Strukturen aus geschweißten Aluminiumprofilen. Für beide Konzepte gibt es gute Gründe.
Lesetipp: Gigacasting – neuer Trend in der Karosseriefertigung für Elektroautos
Zentrale Anforderung: Karosserie muss Mensch und Batterie schützen
Einer, der sich in Deutschland mit der Entwicklung und dem Bau von Elektroautos auskennt wie kaum ein anderer, ist Günther Schuh. Der Professor der RWTH-Aachen hat selbst schon mehrere Elektrofahrzeuge entwickelt und dafür entsprechende Produktionssysteme konzipiert. Seine aktuelle Fahrzeugfirma heißt e.Volution GmbH. Er sagt: „Die Logik des Fahrzeugbaus bekommt ein neues dominierendes Design. Die selbsttragende Karosserie wird dabei abgelöst. Stattdessen nutze ich die Sicherheitsfunktionen, die ich sowieso um die Batterie herum benötige.“ Der Unternehmer verdeutlicht: „Ich muss einen Panzer um die Batterie herum bauen. Das mache ich, erstens um die Batterie zu schützen und zweitens auch um die Passagiere vor der Batterie zu schützen.“ Eine solche Anforderung für die Zulassung habe es beim Bau klassischer Fahrzeuge mit Verbrennungsmotor-Antriebsstrang nicht gegeben.
Der Produktionsexperte verweist auf einen weiteren Aspekt, der für ein neues Karosseriekonzept spricht: „Ich muss die Autos immer so bauen, dass ich die Batterie nicht wie den Verbrennungsmotor im Fahrzeugleben ausnahmsweise mal austausche, sondern regulär mindestens ein oder zweimal im Fahrzeugleben.“ Mit seinem Circular-Car-Konzept verfolgt der umtriebige Wirtschaftsingenieur sogar eine Update-Fähigkeit der Fahrzeuge über einen Zeitraum von 30 Jahren und mehr.
Tesla gelingt es laut Schuh besonders gut, auch die Breite der Karosserie für die Unterbringung der Batterie zu nutzen. „Zum Schutz der Batterie muss der Rahmen dann besonders stabil und eigensteif sein“, macht er deutlich. Damit sei die maßgebliche Struktur der Karosserie vorgegeben.
Was ist der Vorteil von Gigacasting?
Tesla setzt für den Karosserierohbau auf Aluminium-Druckguss. Ziel ist es möglichst wenige, große Teile in einem Schuss herzustellen. In der Branche wird das Verfahren deshalb Giga-, Mega- oder auch Hypercasting genannt. Dabei wird das flüssige Aluminium unter hohem Druck in eine Form gepresst. Statt Seitenteile und Boden aus verschiedenen Teilen zusammenzuschweißen, werden dabei die Funktionen verschiedener Bauelemente in einem Prozessschritt in einem Bauteil vereint. Das spart bei der Montage der Karosserie viel Zeit. Hersteller erhoffen sich dadurch auch Kostenvorteile. Deshalb wollen inzwischen auch Automobilproduzenten wie Toyota und Volvo das Verfahren künftig verstärkt zum Bau von Elektroautos nutzen.
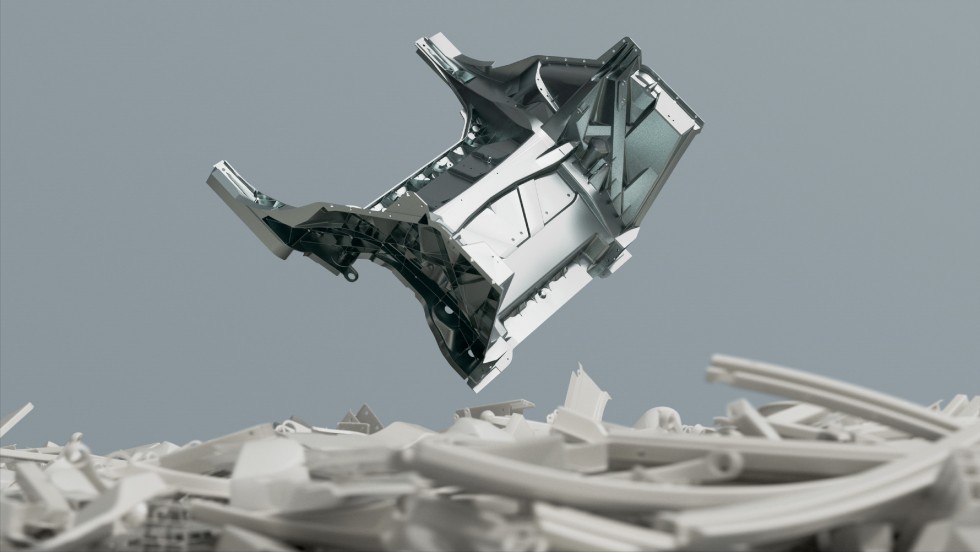
Für den Produktionsexperten Schuh ist das Konzept für Modelle mit großen Stückzahlen von 1 Mio. Fahrzeugen pro Jahr und mehr prädestiniert. „Ich traue Tesla zu, dass sie damit die nächste Welle auch noch schaffen.“ Vielleicht könnten damit sogar 4 Mio. oder 5 Mio. Tesla 2 pro Jahr produziert werden. „Der weltweite Automobilmarkt wird sich künftig bei etwa 100 Mio. Neufahrzeugen pro Jahr einpendeln“, erwartet er. Nur etwa 20 % davon werden aber nach seiner Einschätzung volumenstarke Modelle sein.
Wo liegen die Grenzen beim Gigacasting?
Laut Elektroautospezialist Schuh rechnet sich Gigacasting nur für sehr große Serien, nicht aber für kleinere. So gibt es hohe Werkzeugkosten und bei konstruktiven Änderungen müssten neue Formen hergestellt werden. Zudem gibt er zu bedenken: „Ganze Seiten- und Bodenteile in einem Schuss zu gießen, kommt aus meiner Sicht schnell an Grenzen.“ Eine Karosserie müsse beispielsweise unterschiedliche Festigkeits- und Flächenfunktionen abdecken. Bei Gussteilen seien dafür Kompromisse nötig. „Ein Knotenteil am Fußpunkt der A-Säule braucht eine maximale Festigkeit, wodurch ich dort eine große Materialanhäufung habe. Wenn zudem an der Front noch eine 3 mm dicke blechartige Form entstehen soll, dann kriege ich keine homogene Struktur hin. Außerdem brauche ich einen hohen Druck, um das heiße Aluminium gleichmäßig in der Form zu verteilen“, erklärt der e.Volution-Chef. Dünne und dicke Bereiche ließen sich in dem Fall nicht gleichzeitig optimieren.
Welche Alternative zum Gigacasting gibt es?
Für den Bau solcher Karosserien hält Schuh ebenfalls Aluminium für die richtige Wahl. Für die Optimierung einzelner Bereich und modulare Konzepte sei es aber besser, funktionsähnliche Elemente als Module zu konzipieren. Er plädiert deshalb dafür, Knotenpunkte der Karosserie im Druckguss herzustellen und ansonsten auf standardisierte Stranggussprofile zu setzen. Damit könnten im Vergleich zu den bisher üblichen Stahlblechen auch Kosten für teure Tiefziehformen gespart werden.
Möglich sei die Umstellung auf solche Aluminium-Rahmenkonzepte inzwischen durch Verbesserungen bei den Schweißprozessen. Denn das Bahnschweißen von Aluminium gilt als große Herausforderung. Profile müssen dazu ohne Spalt aneinanderliegen, weil Lücken nicht wie beim Stahl prozesssicher mit Material ausgefüllt werden können. Fachleute nennen das „auf Stoß schweißen“. Die Automobilbranche habe es deshalb lange für unmöglich gehalten, mit einem Aluminiumprofil-Chassis die notwendigen Toleranzen einhalten zu können.
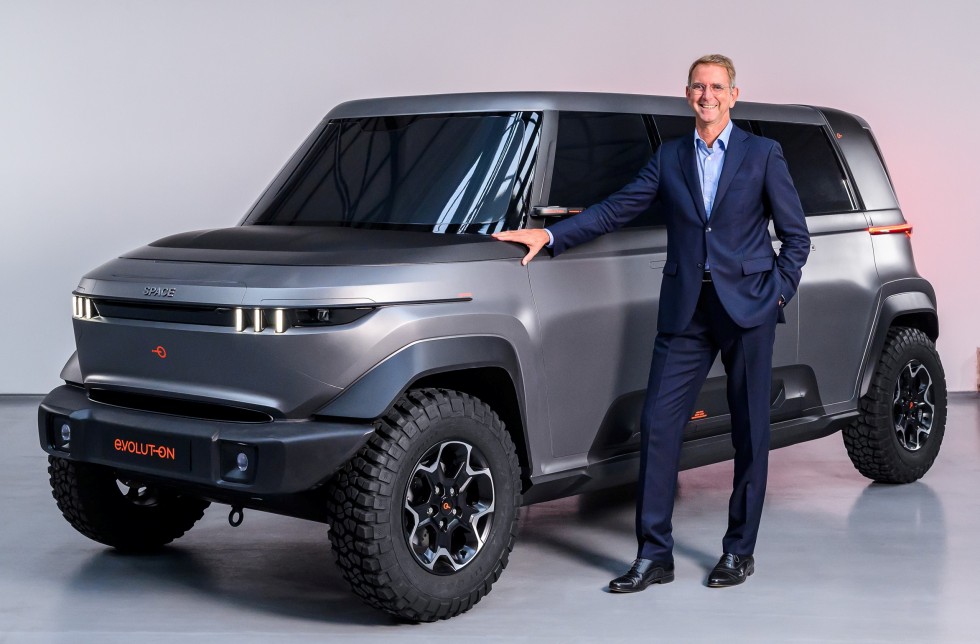
BMW setzt bei Elektro-SUVs auf Aluminiumprofile
Wie das dennoch gelingen kann, hat Schuh mit seinem Elektrokleinwagen eGo inzwischen bewiesen. „Wir haben den per Roboter voll automatisierten Rohbau mit der genialen Firma Lewa Attendorn aus dem Sauerland hingekriegt – und zwar toleranzsicher“, berichtet er. Als großer Automobilkonzern setze inzwischen auch BMW auf eine solche Bauweise. Laut dem Universitätsprofessor habe der Hersteller nun eine Aluminiumplattform für seine Elektro-SUVs der BMW-Modelle iX40 und iX50. „BMW hat es jetzt noch ein bisschen besser gemacht“, räumt er nach einem Besuch in deren Produktion im Vergleich zum Konzept seiner Firma e.Volution ein.
Produktionstechnisch bestehe die Konstruktion aus Frontend, Heck und Mittelteil. Der Toleranzausgleich erfolge beim Anschweißen von Front- und Heckteil. „Da bekommt man eine bessere Toleranzgenauigkeit als heute, mit einer tiefgezogenen Karosserie“, beschreibt er das Ergebnis.
Wenn wir keine alltagstauglichen Elektroautos hinbekommen, die sich die Menschen leisten können, dann werden die Menschen einfach ihre alten Verbrenner länger behalten!
Günther Schuh
Hochschulprofessor und Geschäftsführer der e.Volution GmbH, Aachen
Für Schuh haben solche Karosserien gegenüber großen Gussteilen auch aus einem anderen Grund die besseren Zukunftschancen: „Im Sinne der Nachhaltigkeit brauchen wir viel mehr Standards und viel mehr Modularität, um einzelne Teile und Module zeitgemäß austauschen und upgraden zu können“, sagt er.
Er meint damit nicht nur die Verlängerung der Nutzungsdauer wesentlicher Fahrzeugkomponenten wie der Karosserie und des Elektromotors, sondern auch die Reduzierung der Kosten über den Nutzungszeitraum – die Total Cost of Ownership. Sein Argument: „Wenn wir keine alltagstauglichen Elektroautos hinbekommen, die sich die Menschen leisten können, dann werden die Menschen einfach ihre alten Verbrenner länger behalten!“
Reparatur nach Unfall: Ist Strangguss aus Aluminium die nachhaltigere Lösung?
Mit Blick auf die längere Nutzungsdauer von mindestens 30 Jahren für eine updatefähiges Fahrzeug sagt der Wissenschaftler und Unternehmer: „Schon allein in dieser Zeit passieren zwei bis zweieinhalb kleinere und mittlere Unfälle.“ Bei einer Strukturverformung in einem komplett gegossenen Karosserieteil ließe sich das Auto dann nicht mehr reparieren.
Das dürfte auch für den neuen Cybertruck von Tesla gelten. Denn auch bei dessen Produktion soll das Gigacasting eingesetzt werden. Sind die SUV-Modelle mit modularen Strukturen, wie die von BMW und Schuhs Firma e.Volution, damit die nachhaltigere Alternative zu Teslas neuem Cybertruck? „Ja, unser Fahrzeug ist auf jeden Fall die vernünftigere Lösung“, sagt Schuh.
Cybertruck wird Vorreiter bei Bordnetzen
Trotz einer spürbaren Abneigung gegenüber dem Gesamtkonzept zollt er Elon Musk Respekt für zwei Teilaspekte: „Elektromobilität braucht Emotionalität – und so ein Cybertruck ist schon sehr emotional.“ Außerdem gehe Tesla bei dem Cybertruck mit einer neuen Bordnetzstruktur voran. „Der Cybertruck ist das erste Auto, was eine modulare Architektur mit einem Zentralrechner hat“, erklärt er. Die Subregelung von Aktorik und Sensorik erfolge dabei beispielsweise für den Fensterheber in der Tür. In Verbindung mit einem 48-V-Bordnetz vereinfache das die Struktur. Der Kabelbaum lasse sich viel einfacher montieren, Elemente einfach per Stecker anbinden. Das ist aus seiner Sicht auch für die Update-Fähigkeit von Fahrzeugen wichtig. „Ich mache das mit meinem Konzept beim Meta auch und wäre gerne der Erste gewesen, der das in Serie bringt“, räumt er ein.
Strategisch sei es richtig, dass Musk die neue Bordnetzstruktur zunächst in einer für Tesla-Verhältnisse kleinen Serie zum Einsatz bringe. „Damit übt er diese Struktur für den Tesla 2“, sagt der Produktionsexperte.
Lesen Sie auch: Togg – Neue Konkurrenz für Tesla aus der Türkei