Qualität im Automobilbau auf dem Prüfstand
Teils haarsträubende Sicherheitsmängel lösen weltweit immer größere Rückrufaktionen aus, die nachhaltig am Image der Autobauer nagen. Dass wissen auch Volumenhersteller wie Ford. Die VDI nachrichten haben sich im Kölner Fiesta-Werk angesehen, welche Maßnahmen zur Qualitätssicherung in der Produktionspraxis ergriffen werden.
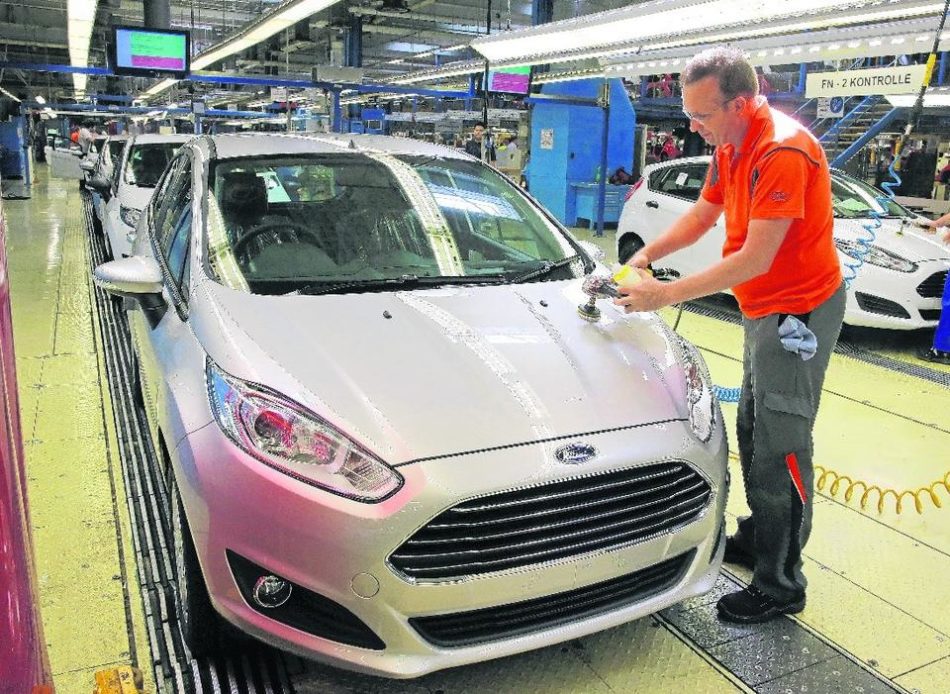
Foto: Ford
Die Automobilindustrie hat in immer größerem Stil mit Rückrufaktionen zu kämpfen, das zeigt nicht nur das Beispiel des Airbag-Rückrufs bei Audi. Zuvor hatte die US-amerikanische Verkehrssicherheitsbehörde NHTSA ebenfalls Alarm geschlagen. Diesmal betrafen die Sicherheitsmängel über 8 Mio. Pkw japanischer, deutscher und amerikanischer Hersteller. Der Grund: Airbags vom japanischen Zulieferer Takata können platzen, Autoinsassen verletzt werden.
Leider keine Einzelfälle: Seit einigen Jahren sind selbst qualitative Musterschüler wie Toyota ins Gerede gekommen. Konzernchef Akio Toyoda musste gar dem US-Kongress Rede und Antwort stehen, weil in den USA aufgrund von klemmenden Gaspedalen Menschen ums Leben gekommen sein sollen. GM kämpft weiter mit den Folgen von „Switchgate“: mindestens 19 Todesfälle infolge von defekten Zündschlössern. Für den Automobilexperten Stefan Bratzel, Leiter des Center of Automotive Management (CAM) an der Fachhochschule der Wirtschaft in Bergisch-Gladbach, ist diese Häufung kein Zufall, sondern u.a. Folge der branchenweit um sich greifenden Baukasten- und Gleichteilestrategie, von kürzeren Modellzyklen und des deutlich gestiegenen Kosten- und Entwicklungsdrucks. „Dieses Damoklesschwert schwebt längst über uns“, sagte der Experte auf Anfrage der VDI nachrichten und warnt: „Das Problem wird uns erhalten bleiben:“
Die vorliegenden Zahlen untermauern dies: Schon nach Ablauf des ersten Halbjahres zählte Bratzel in den USA über 37,2 Mio. zurückgerufene Fahrzeuge, mehr als in den beiden vorangegangen Kalenderjahren zusammen. Mit Blick auf das Gesamtjahr 2014 spricht er von einem „neuen Rekordjahr in Sachen Rückrufe“, nicht zuletzt durch den „Domino-Effekt, der durch GM ausgelöst wurde“. Angesichts der mit Massenrückrufen einhergehenden Kosten- und Image-Risiken für die Autohersteller fordert er „starke Qualitätsmanagementsysteme und entsprechend starke Persönlichkeiten, die dafür Verantwortung tragen“.
Dass Rückrufaktionen das Image einer Marke erheblich schädigen können, weiß man auch bei Ford in Köln, wo täglich 1550 Einheiten des Kleinwagens Fiesta zum Export in über 60 Länder der Erde vom Band laufen. „Safety Recalls können Autofirmen auslöschen“, sagt Gunnar Hermann, Vice President Quality bei Ford Europa. . Qualitätssicherung und -prüfung sowie das Qualitätsmanagement haben für den Hersteller nach eigener Aussage höchste Priorität. Zulieferer würden beispielsweise „Q1-zertifiziert“. Das soll weltweit gleiche Standards an allen Standorten weltweit sichern.
Aber auch in der Produktion wird angesetzt: In der Motorfertigung durchlaufen Kurbelwelle, Zylinderblock und Zylinderkopf zahlreiche Kontrollschritte, bevor sie in die Montagelinien zur Pleuel-, Kolben- und Zylinderkopfvormontage kommen. Dabei finden z. B. Messungen an der mit Haupt- und Pleuellager bestückten Kurbelwelle statt. Im Mikrometerbereich messen Spezialisten hier Durchmesser, Parallelität, Rundlauf und Rundheit. Der Ausschuss beträgt dabei laut Hersteller weniger als 2 %. Pro Schicht wird zusätzlich ein Teil mit einem Koordinatenmessgerät akribisch auf Maßhaltigkeit überprüft. Gemessen wird auf Tausendstel mm genau, und zwar bei einer Normtemperatur von 20 Grad C. Aus gutem Grund. Ein Zylinderkopf beispielsweise unterliegt pro Kelvin einer Ausdehnung von rund 5 µm. In der Schattenmessstation lassen sich darüber hinaus berührungslos und hochpräzise beispielsweise Schraubengewinde überprüfen. Jedes größere Bauteil trägt einen maschinell registrierten Code, mit dem sich alle Parameter wie Charge und Produktionszeit auslesen und im Notfall rückverfolgen lassen.
Rund jeder zwanzigste der fertig montierten Motoren muss sich neben einem „Cold Test“, bei dem das Aggregat durchgedreht wird, auch einem „Hot Test“ unterziehen. Dazu wird der Motor gestartet, sämtliche Funktionen von Motor und Einspritzung werden überprüft. Öllecks entlarvt eine Schwarzlichtprüfung, bei der das im Öl enthaltene Kontrastmittel luminisziert. In Stichproben werden Motoren zerlegt und vermessen, andere müssen sich einem 100-h-Dynamometer-Teststandlauf unterziehen. Das entspricht 20 000 km – 30 000 km im Realfahrbetrieb.
Um bei der die Fülle von Einzelmaßnahmen den Überblick zu behalten, hat Ford ein sogenanntes „Quality-Leadership-System“ (QLS) implementiert, in dem alle Auffälligkeiten erfasst werden – sowohl von Stationen mit manueller und visueller Prüfung als beispielsweise auch von mehr als 300 elektronischen Schraubwerkzeugen, die Informationen an das System schicken. Sie melden, wenn an einem Fahrzeug die Verschraubung nicht in Ordnung ist.
Ist ein Fahrzeug fertig montiert, werden die Antriebe vor der Auslieferung auf einem Rollenprüfstand abermals getestet. Dort wird das Fahrzeug auf 120 km/h bis 130 km/h beschleunigt. Auch das Getriebe muss seine einwandfreie Funktion unter Beweis stellen, die Signalanlage und die Beleuchtung testen die Mitarbeiter ebenfalls. Anschließend rollt der Fiesta in die „Customer Acceptance Line“, wo die Türpassungen gesetzt und die Passgenauigkeit von Türen, Motorhaube und Heckklappe per Lasertechnik vermessen werden. Ein Lichttunnel entlarvt Unregelmäßigkeiten an der Außenhaut, sowie im Innenraum und unter der Motorhaube. Anschließend steht der Wassertest an, bei dem die Fiestas mehrere Minuten einem Wasserdruck von 1,2 bar ausgesetzt werden, um die Dichtigkeit der Fahrzeuge zu prüfen.
Aber auch das „Popometer“ und sonstige menschliche Sinneswahrnehmungen haben als Kontrollinstanz längst noch nicht ausgedient: Das erste Mal das Licht der Autowelt erblickt der Kleinwagen auf seinem Weg zum Außengelände, wo speziell geschulte Fahrer auf der „Squeak-and-Rattle-Strecke“ auf zehn verschiedenen Untergründen testen, ob es Geräusche gibt, die zu beseitigen wären.
Ist dies der Fall, geht es für das betreffende Fahrzeug auf einen Hydropulser. Dort steht es auf vier Hydraulikstempeln, die verschiedene Arten von Stößen simulieren. Offenbar mit Erfolg: „In zehn Jahren haben wir die Aufwendungen für Garantieleistungen halbieren können“, sagt Gunnar Hermann. Regelmäßig würden zudem Kunden, die kürzlich ein Neufahrzeug erhalten haben, befragt. ihre Rückmeldung wird anschließend sowohl für die Entwicklung neuer Fahrzeuge als auch für Veränderungen am aktuellen Modell berücksichtigt.
Allerdings: Eine 100%ige Garantie gegen Rückrufe ist auch das nicht, das weiß Ford, in diesem Jahr selbst von einem Millionenrückruf in den USA betroffen, so gut wie die Wettbewerber. Dazu, heißt es, sei das Gesamtsystem „Automobil“, seine Entwicklung und Produktion, inzwischen schlichtweg zu komplex.
Hier finden Sie die Studie von Stefan Bratzel