Druck auf die Ersatzteillogistik
Additive Manufacturing (landläufig "3D-Druck") ist in der Industrie angekommen. Selbst in Flugzeug- und Kraftwerkturbinen sind gedruckte Bauteile im Serieneinsatz. Hersteller träumen laut von einer Service- und Wartungswelt, in der sie Ersatzteile vor Ort drucken und etwaige Defekte in "Rapid-Repair-Prozessen" beheben.

Foto: Siemens
Fernando Rodriguez ist gespannt, was ihn bei dieser Revision erwartet. Obwohl sein Team schon begonnen hat, den 15-stufigen Axialverdichter der 290-MW-Gasturbine freizulegen, weiß der Ingenieur noch nicht, welche Ersatzteile sie benötigen werden und welche Reparaturen anstehen. Als der Argentinier in den 2000er Jahren seine ersten Turbinenrevisionen erlebte, war solche Spontaneität undenkbar. Wochenlang bereiteten sie Revisionen seinerzeit vor. Inspizierten, werteten Betriebsdaten akribisch aus – und vor allem orderten sie vorab palettenweise Ersatzteile aus dem Zentrallager in Deutschland. Es war üblich, hoch belastete Komponenten turnusmäßig auszutauschen, wenn ihre Betriebsstunden voll waren. Ganz unabhängig von ihrem tatsächlichen Zustand.
Heute, im Frühherbst 2030, läuft das anders. Wo immer auf dem südamerikanischen Kontinent sich Rodriguez mit seinem Expertenteam an die Wartung, Reparatur oder Revision einer Turbine macht, können sie auf lokale Additive Manufacturing Zentren zugreifen. In den firmeneigenen Zentren lassen sie Komponenten, die ihrer Prüfung nicht standhalten, über Nacht aus entsprechenden Legierungen nachbauen. Genauer werden sie Schicht für Schicht aus Pulver dieser Legierungen aufgebaut. Dafür fährt ein Dutzend Laserköpfe die Bauteilkontur ab und bringt jeweils frisch ausgebreitetes Pulver zur Schmelze. Anschließend wird das Teil um einige µm abgesenkt, frisches Pulver ausgebreitet und der Tanz der Laser beginnt aufs Neue.
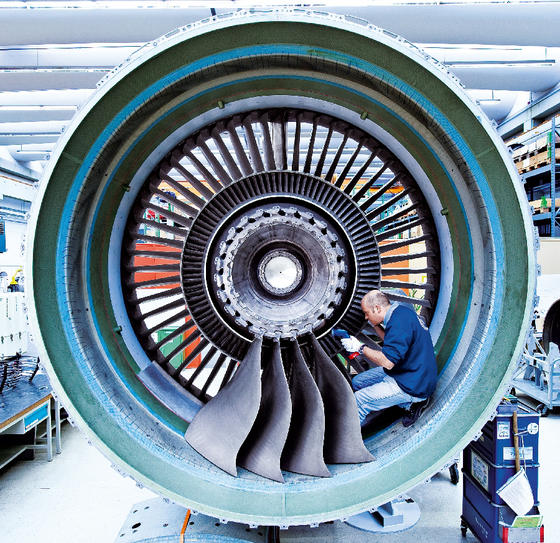
Den Weg übers Pulverbett weist den Lasern die 3D-Konstruktionsdatei des Original-Bauteils. Um sie samt zugehörigen Prozessdaten vom Zentralserver abzurufen, muss Rodriquez neben persönlichem Passwort und Projektnummer die Bauteil-ID und die Seriennummer der Turbine eingeben. Erst dann steht eine verschlüsselte Datei zum Abruf bereit, die er nur per Decoder mit individueller PIN-Eingabe öffnen kann. Nach dem 3D-Ausdruck wird sie automatisch gesperrt: Datensicherheit ist Trumpf, wo sich Originalbauteile aus Dateien ausdrucken lassen.
Sieht so die Zukunft der Ersatzteillogistik aus? Werden Service- und Wartungstrupps vor Ort Ersatzteile „on-demand“ drucken, statt sie vorab um den halben Globus zu verschiffen oder eilig per Luftfracht heranzuschaffen? Bei Siemens denken sie sehr konkret über solche Szenarien nach. Schon in fünf bis zehn Jahren will die Kraftwerkssparte des Konzerns Brennerköpfe, Einspritzdüsen oder die mit einem Netz von Lüftungskanälen durchzogenen Turbinenschaufeln im oben beschriebenen
Selective-Laser-Melting-(SLM)-Prozess fertigen. Noch laufen laut Andreas Fischer-Ludwig, Standortleiter des Siemens-Gasturbinenwerks in Berlin, Lebensdauertests solcher additiv gefertigter Komponenten. Geht es nach ihm, wird das SLM-Verfahren sehr bald Basis eines Servicegeschäfts sein, in dem „Print-on-demand“ und „Repair-on-demand“ die Ausfallzeiten von Kraftwerken minimieren. „Die Technologie hat das Potential zum Gamechanger“, sagt er.
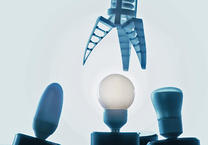
Schon heute nutzt der Konzern das additive Verfahren, um abgenutzte Brennerköpfe von Gasturbinen aufzubereiten. Dafür werden die defekten Bereiche abgetrennt und per SLM neu aufgebaut. „Wir sind dadurch um den Faktor 10 schneller, verbrauchen 60 % weniger Material und können die Kosten der Wiederaufarbeitung um fast ein Drittel senken“, so Fischer-Ludwig. Statt bisher 44 Wochen dauere das Instandsetzen ganzer Sets, die je nach Turbinentyp aus über zwei Dutzend Brennerköpfen bestehen können, nur noch vier Wochen. Mit heutiger Anlagentechnik wohlgemerkt, die in aller Regel mit nur einem Laserkopf arbeitet. Doch das ändert sich. So hat die SLM Solutions aus Lübeck als erster Anlagenbauer Laserstrahlschmelz-Anlagen im Markt, in denen zwei oder sogar vier Köpfe das Pulver schmelzen. Theoretisch können sie Bauteile doppelt oder sogar viermal so schnell wachsen zu lassen, wie die bisherige Technik. Doch hält die Abkühlphase der fertigen Teile den Prozess auf. Hier sollen Wechselsysteme Abhilfe schaffen, in denen die Bauteile extern abkühlen, während in der Anlage der nächste Fertigungsprozess beginnt.
Eine weitere Option zur Produktivitätssteigerung sieht Dieter Schwarze, Leiter des Bereichs Additive Prozesse bei SLM in Lübeck, in der Kombination verschieden starker Laser. Zur Veranschaulichung nutzt der promovierte Physiker das Bild von Quast und Pinsel. Ein 1000-W-Laser könne als „Quast“ Fläche machen, während ein 400-W-Laser als „Pinsel“ die feinen Konturen zeichne. Wobei „Fläche“ in diesem Fall 700 µm breite Schmelzspuren im Metallpulver bezeichnet, während der 400-W-Laser siebenmal feinere Spuren zieht. Schwarze, der den SLM-Prozess in den 1990er Jahren maßgeblich mitentwickelt hat, hält es für möglich, die Aufbauraten mit derart kombinierter Laserleistung um den Faktor 5 gegenüber dem Status-Quo zu steigern. Zudem erwartet er, dass es in Zukunft Anlagen mit noch mehr Laserköpfen geben wird, die beschleunigte Fertigung großer Bauteile erlauben werden. Hier komme es darauf an, dass im Überlappbereich der einzelnen Köpfe keine Fehler im Bauteil auftreten, etwa weil Lücken bleiben.

Lösbare Probleme, die für junge Technologien typisch sind. Nicht minder typisch findet es Heiner Lasi, der am Lehrstuhl für Allgemeine Betriebswirtschaftslehre und Wirtschaftsinformatik I der Universität Stuttgart forscht und lehrt, „dass das Additive Manufacturing bisher primär technologisch getrieben ist. Geschäftsmodelle und IT-Infrastrukturen hinken hinterher“, erklärt der promovierte Wirtschaftsinformatiker. Er befasst sich schwerpunktmäßig mit der Veränderung von Geschäftsmodellen im Zuge der Industrie 4.0 und des Additive Manufacturing. Nach seiner Auffassung muss sich gerade die Logistikbranche darauf einstellen, dass ihr Geschäft durch die orts-, zeit- und Knowhow-unabhängige Print-on-demand-Fertigung erodieren könnte.
Braucht es noch Ersatzteillager, die zehntausende Bauteile in vielfacher Ausführung vorhalten und rund um die Uhr bereitstehen, um eilige Ersatzteile ans andere Ende der Welt zu versenden? Besonders schwierig, da zeitkritisch und schwer planbar, ist die Ersatzteilversorgung der zivilen Luftfahrt. Standzeiten großer Passagierflugzeuge kosten 100 000 € pro Tag; müssen Passagiere in Hotels untergebracht werden, kommt schnell die doppelt und dreifache Summe zusammen. Entsprechend bemüht sich die Branche, unerwarteten Ausfällen durch präventive Wartung und sehr enge Inspektionszyklen zu begegnen. Doch weil Flugzeuge ständig unterwegs und dabei durch Verzögerungen und Verschiebungen von Flügen oft umgeleitet werden, bleibt der Ort der nächsten turnusgemäßen Wartung lange vage. Dennoch müssen zur rechten Zeit alle benötigten Ersatz- und Austauschteile am rechten Ort bereitstehen.
Ein teures Unterfangen: Experten schätzen, dass Fluggesellschaften rund ein Zehntel ihrer Betriebskosten für die Lagerung und Just-in-Time-Lieferung von Ersatzteilen aufwenden. Totes Kapital, das in Hochregalen in den Sicherheitsbereichen von Flughäfen lagert und an dem zu allem Überfluss der Zahn der Zeit nagt: überalterte Ersatzteile dürfen nicht oder nur nach erneuter Zertifizierung verbaut werden.
Vor diesem Hintergrund verwundert es nicht, dass Flugzeugbauer und ihre Zulieferer zu den ersten Anwendern additiver Fertigung gehören. Vorerst begründen Airbus und Boeing den Einsatz mit Gewichts- und Kostenvorteilen. Der 3D-Druck erlaubt ihnen bionische Konstruktionen mit dem Werkstoff Titan, die bis zu zwei Drittel Gewicht sparen und bisher nicht oder nur mit hohem Kosten- und Materialaufwand zu fertigen waren. Während solche additiv gefertigten Strukturbauteile im gesamten Flugzeug verteilt sind – bei Boeing sind es über alle Flugzeugtypen hinweg schon über 20 000 solcher Komponenten – setzen auch Triebwerkbauer verstärkt auf schichtende Verfahren. So realisiert GE Aviation Einspritzdüsen per 3D-Druck aus einem Teil, die bisher aus 30 Einzelteilen montiert werden mussten. Obendrein sind sie 25 % leichter und halten den hohen Temperaturen im Triebwerk besser stand.
Auch der Triebwerksbauer MTU Aero Engines fertigt bereits Serienteile im SLM-Prozess: sogenannte Boroskopaugen. Durch diese Bauteile werden optische Systeme eingeführt, um ins Innere des Triebswerks vom Airbus A320neo schauen zu können. Weitere Triebwerkskomponenten sollen folgen, darunter Schaufeln und Dichtelemente für die Hochdruckverdichter der besonders effizienten und leisen Getriebe-Fantriebwerk-Baureihe. MTU entwickelt sie zusammen mit US-Hersteller Pratt&Whitney. „Wir entwickeln das additive Verfahren aktuell mit hoher Priorität weiter“, so MTU-Technikvorstand Rainer Martens.
Jedes additiv produzierte Bauteil, das es aus den F&E- und Konstruktionsabteilungen in die Serienfertigung der Flugzeug- und Kraftwerkbauer schafft, ebnet den Weg zu einer weltweiten Ersatzteilversorgung ohne Logistik. Wegen der hohen Ausfallkosten haben beide Branchen größtes Interesse an einer Service- und Wartungswelt, deren Ersatzteile jeweils vor Ort ausgedruckt werden. Perspektivisch sollen Server mit 3D-Files Ersatzteillager und aufwändige Transportketten ersetzen. Weitere Branchen werden folgen, wenn die additiven Fertigungsprozesse technologisch reifen und die Kosten der Anlagen und Metallpulver sinken. Wirklich fraglich ist aus heutiger Sicht eigentlich nur, ob Fernando Rodriguez und sein Team 2030 zu den Pionieren der 3D-druckenden Servicezunft gehören werden – oder doch eher schon zum Mainstream.
Ersatzteile aus dem Drucker
Laserstrahlschmelzen ist nur eines von vielen Verfahren des Additive Manufacturing. Damit lassen sich Metalle wie Aluminium, Titan oder Stähle verarbeiten. Vorteil: Anderes als beim Guss braucht es keine Formen und gegenüber spanenden Verfahren ist die Materialeffizienz höher. Zudem lassen sich sehr komplexe Bauteile mit Hohlräumen, Kanälen und variierenden Wandstärken fertigen, da die Bauteile im Prinzip aus gestapelten 2-D-Schichten bestehen.
Eine Alternative zum Ausdruck von Metall-Ersatzteilen hat der deutsch-japanische Maschinenbauer DMG Mori kürzlich vorgestellt: Die Anlage kombiniert Laserauftrag-Schweißen und 5-Achs-Fräse und wechselt jeweils voll automatisch zwischen Laser- und Fräsbetrieb. Vorteil ist die 20 x höhere Geschwindigkeit.
Neben dem 3-D-Druck von Metallen gibt es diverse Kunststoffverfahren. Zuvorderst das Lasersintern. Laser gesinterte Bauteile sind u.a. in der Robotik und Handhabungstechnik im Serieneinsatz. Vorteile auch hier: Leichtbau, Funktionsintegration und schnelle Verfügbarkeit von Ersatzteilen. Neben dem Lasersintern gibt es etliche Extrusionsverfahren, die Bauteile aus feinen Kunststoffsträngen oder Tröpfchen aufbauen sowie die Stereolithographie, bei der gezielt eingebrachte UV-Strahlen Bauteile im Bad aus UV-härtendem Kunststoff entstehen lassen.