Container aus dem Hochregal
Der Platz im Hafen ist begrenzt, aber das Frachtvolumen nimmt zu. Ein Konzept aus der Stahllogistik könnte das Problem nun lösen.
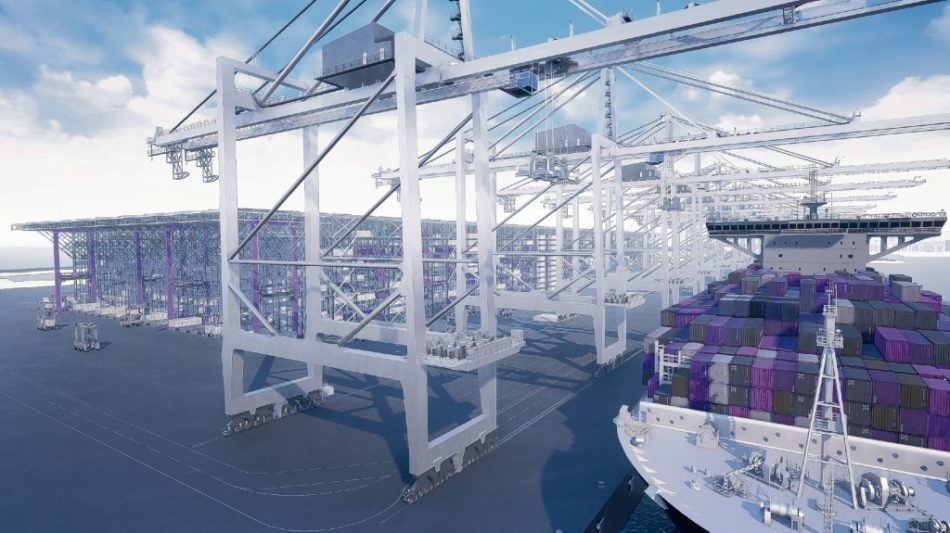
Foto: SMS group
Ein riesiges Hochregallager entsteht derzeit in Dubai. Das Besondere: Statt kleiner Boxen oder einzelner Produkte sollen darin ganze Überseecontainer elf Etagen hoch übereinander gestapelt werden. Noch werden die riesigen Frachtboxen beim Löschen der Ladung auf dem Hafengelände einfach aufeinandergesetzt – bis zu sechs übereinander. Das Problem: Bisher müssen die Container umgestapelt und entsprechende Flächen vorgehalten werden. Das Umstapeln macht zwischen 30 % und 60 % der Containerbewegungen aus. Eine Technik, die ursprünglich für vollautomatisierte Prozesse in der Logistik von Stahlprodukten entwickelt wurde, soll das künftig ändern und Hafenbetreibern zusätzliche Flexibilität verschaffen.
Das scheint dringend nötig. Denn während in Dubai ein Terminal quasi auf der „grünen Wiese“ entsteht, steigt der Druck auf bestehende Hafenanlagen und -betreiber. Sie müssen auf steigende Frachtraten ebenso flexibel reagieren wie auf Verschiebungen in Lieferketten (s. Beitrag re.). „Die meisten großen Seehäfen sind historisch gewachsen und grenzen an Hafenstädte an“, weiß Mathias Dobner, CEO von Boxbay. „Die Topologie setzt dem Ausbau dieser Häfen Grenzen. Hinzu kommen immer strengere Umweltauflagen – insbesondere für Aufschüttungen“, berichtet er. Mit der neuen Lösung wolle sein Unternehmen dafür Perspektiven schaffen. Das Konzept sei skalierbar und schaffe bereits mit dem ersten Modul zusätzliche Kapazitäten.
Voll automatisiert und modular erweiterbar
Die Firma Boxbay ist eine Kooperation von DP World aus Dubai, einem der weltweit größten Hafenbetreiber, und dem deutschen Maschinen- und Anlagenbauer SMS Group aus Düsseldorf. Mit der gebündelten Kompetenz wollen die beiden Unternehmen schaffen, was anderen Lösungsanbietern bisher nicht gelungen ist. Sie wollen ein durchgängig automatisiertes Containerterminal auf Basis von Hochregallagern aufbauen, das modular erweitert werden kann und sich für die Betreiber schnell rechnet.
Grundlage dafür bildet eine Technik, die die SMS-Tochter Amova ursprünglich für die Stahlwerklogistik entwickelt hat. Dort werden bereits seit einigen Jahrzehnten bis zu 50 t schwere Rollen mit Stahlblechen vollautomatisiert in Hochregallagern untergebracht. Bis zu 4288 der teilweise noch heißen Coils werden dabei in den High-Bay-Storage-Systemen (HBS) eingelagert.
Erfahrung mit Logistikanlagen
Die Erfahrungen kommen auch der Luftfracht zugute. Im Sommer beginnt das Unternehmen den Bau der neuen Logistikanlage des Frachtterminals am Flughafen Manchester. Kompetenzen mit dem Bau von Logistikanlagen sowie der Steuerung der Logistikprozesse bis hin zur animierten Echtzeitvisualisierung der automatisierten Transporttechnik inklusive autonomer Fahrzeuge sind also in unterschiedlichen Anwendungen bereits belegt. Doch wie sieht die Lösung für die großen Überseecontainer aus?
Gelöscht werden die Containerschiffe wie bisher mit riesigen Portalkränen, den sogenannten Containerbrücken. Anschließend übernehmen bemannte oder unbemannte Fahrzeuge den Weitertransport zum Hochregallager. Das können Portalhubwagen, Auflieger-Lkw (Terminal Trucks) oder fahrerlose Transportsysteme sein. An der Aufnahmeposition des Boxbay-Systems übernehmen Hochregalbediengeräte die Container. Ein Stapelkran (Stacker Crane) dockt dazu von oben an den vier Ecken des Containers an. Dort gibt es standardisierte Drehzapfenaufnahmen für die Verriegelung. Weil sowohl 20-Fuß-Container als auch 40-Fuß-Container umgeschlagen werden, erfolgt dazu eine automatische Längenanpassung. Parallel zum in Dubai laufenden Lageraufbau wurden die Regalbediensysteme bereits im Fertigungswerk gebaut und getestet.
Keine Regalböden
Und so läuft der Prozess im fertigen Hochregallager dann weiter: Wurde die Fracht erfolgreich übernommen, wird sie über die Gänge zu einem Regallagerplatz transportiert. Auf dem Weg im Gang des Hochregallagers wird der Container parallel bereits auf die Ebene seines Regalfaches hochbefördert. Das spart Zeit. Mit ihren Teleskoparmen erreichen die Stapelkrane Regale auf beiden Seiten. Anders als bei üblichen Hochregallagern gibt es dort keine Regalböden, denn die Container sind selbsttragend. Das reduziert die Materialmenge und damit das Gewicht der Regalsysteme, ohne die Statik zu schwächen.
Die Lagerplatzwahl wird von der Anlagensteuerung übernommen. Diese sorgt beispielsweise dafür, dass schwere Container auf unteren Ebenen gelagert werden und leichte Container in die oberen Etagen befördert werden – so wie es auch bei der Ladung der Frachter erforderlich ist. Auch Besonderheiten wie Kühlcontainer können in der Software berücksichtigt werden. Denn sie müssen über zusätzliche Anschlüsse mit Energie versorgt werden und sollen idealerweise nicht der prallen Sonne ausgesetzt werden. Dafür mussten die Entwickler lediglich die Programmierung des bereits in der Coil-Logistik eingesetzten Trackingsystems auf die neuen Anforderungen anpassen. Darin lassen sich alle Positionen im Betrieb zurückverfolgen.
In der Coil-Logistik erprobte Abläufe
Die Entnahme der Container sowie deren Abtransport erfolgt nach in der Coil-Logistik bereits erprobten Abläufen. Unter dem Boden der Regalgänge gibt es automatisch auf Schienen fahrende Paletten. Darauf wird die Fracht abgestellt und energieeffizient zum Übergabeplatz gebracht, wo sie von handelsüblichen vollautomatischen Containerkränen übernommen und auf Lkw oder Züge verladen wird. Regalbediensysteme und Unterflurpalettenumlaufsystem können arbeiten, ohne sich gegenseitig zu blockieren.
Darüber hinaus können auf diese Weise Übergabepositionen auf allen vier Seiten des Lagersystems angebunden werden. Die damit realisierte vollständige Entkopplung der Materialflüsse verschafft dem System eine hohe Flexibilität und sorgt nach Boxbay-Angaben für bisher unerreicht hohe Durchsatzleistung pro Fläche. Nach vom Unternehmen durchgeführten Simulationen einer Referenzanlage, lassen sich dabei mehr als 500 wasserseitige und 300 landseitige Containerbewegungen gleichzeitig durchführen.
Frachtschiffe werden immer größer
Gerade für die großen Häfen der Welt dürfte das eine wichtige Kenngröße sein. Denn die Frachtschiffe werden immer größer. Um die Jahrtausendwende waren klassische Containerschiffe für etwa 8000 TEU ausgelegt. Eine TEU entspricht einem 20-Fuß-Container nach ISO-Standard. Heute erreichen die größten Schiffe Kapazitäten von bis zu rund 24000 TEU. Selbst bei den großen 40-Fuß-Containern (2 TEU) dauert das Löschen und Stauen im Hafen mehrere Tage. Jeder gesparte Tag ist dabei bares Geld für die Reedereien und die Hafenbetreiber.
Für Burkhard Dahmen, den CEO der SMS group, ist Boxbay „eine disruptive Innovation, die sowohl in der Umschlagkapazität, der Raumkapazität als auch in der Digitalisierung neue Maßstäbe in der Hafenlogistik setzt“. Er geht ebenso wie die Projektpartner bei DP World davon aus, dass die Lösung bisherige Systeme ablösen wird. Neben den schnellen Prozessen auf kleinem Raum ist für ihn der direkte Zugriff auf einzelne Container ein wesentlicher Vorteil des High Bay Systems.
System mit Zukunftschancen
Auch die Hafenlogistikspezialisten von DP World sind nach zahlreichen Erkenntnissen mit unterschiedlichen Hafentechnologien von den Zukunftschancen des Systems überzeugt. Sultan Ahmed Bin Sulayem, Chairman und CEO von DP World Group, sagt: „Wir sind von Boxbay begeistert, da es die Geschwindigkeit und Effizienz des Umschlags steigert. Das sind die Schlüsselfaktoren des Hafen- und Terminalgeschäfts.“ Für ihn gehört das System damit zu den wichtigsten Entwicklungen für Häfen auf der ganzen Welt.
Nebenbei könnten derartige Containerterminals auch für ein besseres Klima im Hafen sorgen. Denn das Konzept sieht vor, das Lager mit Solarzellen zu bedecken und teilweise zu begrünen. Neben dem dadurch gewonnenen Strom soll Bremsenergie aus den Elektroantrieben zurückgewonnen werden. Gleichzeitig könnte durch die Vollautomatisierung weitestgehend auf eine Beleuchtung verzichtet werden, heißt es vom Boxbay-Projektteam. Dadurch werde einerseits Energie gespart, andererseits auch die Lichtverschmutzung reduziert, die sich in der Regel störend auf Tagesabläufe von Menschen und Tieren auswirkt.
Know-how in neue Anwendungsbereiche bringen
Das Beispiel kann Anlagenbauern aus anderen Bereichen Mut machen. Denn es zeigt, wie die bisher stark mit der Stahl- und Metallbranche verbundene SMS-Gruppe sich mit bestehendem Know-how neue Anwendungsbereiche erschließt und unabhängiger vom von Überkapazitäten geprägten Stahlgeschäft wird.
Bei Hochregalsystemen will man sich weiter auf große und schwere Produkte fokussieren und nicht mit Anbietern von konventionellen Distributionslogistiklösungen konkurrieren. Die Containerlogistik mit Lasten bis zu 32 t schließt dabei die Lücke zwischen dem Handling von Stahlprodukten mit bis zu 50 t und den Luftfrachtcontainern mit bis zu 8 t.
Wer steckt hinter Boxbay?
- Boxbay ist ein Joint Venture der SMS Group aus Düsseldorf und der DP World aus Dubai.
- SMS group ist eine Gruppe international tätiger Unternehmen des Anlagen- und Maschinenbaus, insbesondere für die Stahl- und NE-Metallindustrie. Die Gruppe beschäftigt weltweit 14 000 Menschen und erwirtschaft einen Umsatz von über 2,8 Mrd. €. Alleineigentümer der Holding SMS GmbH ist die Familie Weiss Stiftung.
- DP World ist aktiv in Geschäftsbereichen, die von See- und Binnenlandterminals, maritimen Services, Logistik und Zusatzdienstleistungen bis hin zu technologieorientierten Handelslösungen reichen. Kerngeschäft ist der Containerumschlag, mit dem 50 % des Gesamtumsatzes erwirtschaftet werden. Das Unternehmen beschäftigt insgesamt mehr als 46 000 Menschen in 120 Ländern.