Hochzeit der Bohrroboter
Mit einer vierten Endmontagelinie in Hamburg will Airbus die Produktion seiner A320-Familie um 25 % steigern. Noch bremsen aber Triebwerksprobleme den europäischen Flugzeugbauer.

Foto: Wolfgang Heumer
Wenn das Stichwort Hochzeit fällt, leuchten „Luise“ und „Renate“ rot auf. Nicht etwa, weil ihnen das Thema missfiele: „Luise“ und „Renate“ sind die beiden Roboter, die im Hamburger Airbus-Werk an der neuen und vierten Fertigungslinie die vordere und hintere Sektion eines neuen Airbus aus der A320-Familie zusammenfügen. Auf den weltweit sieben weiteren Fertigungsstraßen des Erfolgsflugzeuges wird dieser Prozess – im Flugzeugbauerjargon Marriage (Hochzeit) genannt – noch manuell vollzogen. „Mir ist auch von anderen Herstellern nicht bekannt, dass jemand das wie wir vollautomatisch macht“, sagt Frank Rocksien, Chef der neuen und vierten A320-Fertigungslinie in Hamburg-Finkenwerder.
Der Drang zu neuen Fertigungsmethoden kommt beim europäischen Flugzeugbauer nicht von ungefähr. Die A320-Familie mit nur einem Kabinengang (single aisle) und vier verschiedenen Größen (A318 bis A321) ist der Verkaufsschlager schlechthin. Statt der bei der Entwicklung im Jahr 1988 geplanten 700 Exemplare wurden mittlerweile 8150 Stück ausgeliefert – weitere 6078 Flugzeuge stehen im Orderbuch. Derzeit fertigt Airbus in Hamburg, Toulouse, Mobile (USA) und Tianjin (China) insgesamt 50 Flugzeuge pro Monat. Mit der vierten Produktionslinie in Finkenwerder soll der Output in Hamburg von 30 auf 40 Maschinen und weltweit damit auf 60 gesteigert werden. „Wir müssen Gas geben“, sagt Klaus Röwe, der das A320-Programm verantwortet.
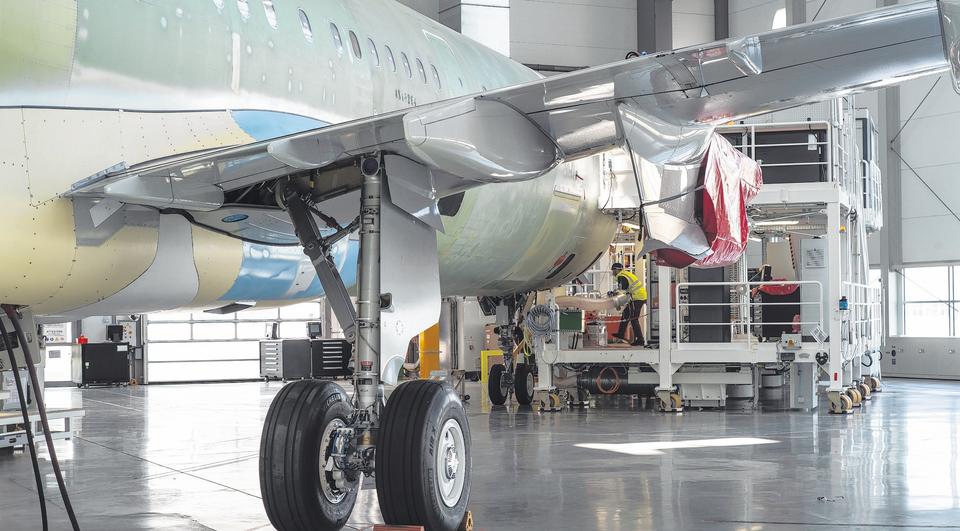
Innerhalb von 14 Monaten entwickelten und bauten die Hamburger die vierte Endfertigung. Um dieses Tempo überhaupt zu schaffen, integrierten sie die neue Linie in einen alten Hangar. „Sonst hätte schon allein der Bau der Halle viel länger gedauert“, so Röwe. Dafür nahmen die Planer in Kauf, dass die Flugzeuge nicht mehr in gerader Linie gebaut werden können, sondern von Station zu Station mehrere Kurven – einmal sogar um 180 Grad – fahren müssen.
Möglich wird dies durch die neue weitgehend automatisierte Fertigungstechnik, an die sich zuvor kein anderer Flugzeugbauer herangetraut hat. An der ersten Station setzen die beiden 7-Achs-Roboter „Renate“ und „Luise“ auf der rechten bzw. linken Rumpfseite etwa 80 % der für die „Hochzeit“ erforderlichen Bohrlöcher. Anschließend manövriert eine autonome mobile Arbeitsplattform den Rumpf selbstständig zu den insgesamt sechs Fertigungsstationen. Zwei weitere Plattformen bringen – ebenfalls automatisch – die vorgefertigten Flügel in die richtige Montageposition. Überall werden Positionen und Maße mithilfe eines dynamischen Vermessungslasersystems überwacht und kontrolliert. Die Herausforderung war nicht das Konzept an sich: „Wir mussten ein Fertigungsverfahren aus der Industrie 4.0 an ein Flugzeug anpassen, dessen Design vor 30 Jahren entwickelt worden ist“, so Röwe.
An der Entwicklung der neuen Fertigungslinie sind die dort Beschäftigten laut Airbus maßgeblich beteiligt worden. In das Konzept flossen nicht nur ihre Erfahrungen ein – auch die Mitarbeiter selbst entwickelten sich weiter. Schließlich sollen sie nicht nur parallel zu den Robotern, sondern gemeinsam mit ihnen arbeiten. „Früher waren sie Mechaniker, heute sind sie Mechaniker und Operator zugleich“, betont Rocksien. Für ihn sind die Fachkräfte schon wegen ihrer Erfahrung unverzichtbar. Bei einem Probelauf von „Renate“ und „Luise“ habe einer der Mechaniker allein durch das Bohrgeräusch erkannt, „dass der Bohrer nicht scharf genug war“, erinnert sich Rocksien. „Keiner hat es ihm geglaubt, bis wir das Ergebnis unter dem Mikroskop kontrolliert haben.“
Mit 180 Personen im Zwei-Schicht-Betrieb sind an der neuen Linie nur geringfügig weniger Mechaniker beschäftigt als in den drei traditionellen Endmontagen. „Diese Entwicklung ist ein überaus wichtiger Meilenstein für den gesamten Airbus-Konzern“, lobt Guillaume Faury, Präsident des zivilen Luftfahrtbereiches von Airbus.
Allerdings bremst eine Altlast aus der jüngeren Vergangenheit den Vorwärtsdrang der europäischen Flugzeugbauer. Monatelang konnte Airbus insbesondere das jüngste Modell A320neo nicht ausliefern, weil es technische Probleme mit den Pratt-&-Whitney-Triebwerken gab. „Wenn wir von der Tragweite des Problems früher informiert worden wären, hätten wir die Produktion gedrosselt“, sagt Röwe rückblickend.
In Ermangelung dieser Informationen produzierten die Hamburger munter weiter – an mehreren Stellen des Werksgeländes stehen seither Dutzende fertig montierte Flugzeuge ohne Triebwerke herum. „Dieses Problem werden wir bis Ende des Jahres abgearbeitet haben“, ist Röwe optimistisch. Es werde jedoch noch wesentlich länger dauern, den darüber hinaus aufgelaufenen Produktionsstau abzuarbeiten. Kleiner Trost für Kunden: Airbus hat in Hamburg parallel zur neuen Fertigungslinie die Atmosphäre geschaffen, um sie zu besänftigen. Speziell für die A320-Familie wurde ein neues Auslieferungszentrum eingerichtet.