„Die Triebwerke werden immer größer“
Die Zahl der Fluggäste steigt rapide an – in der Luftfahrtindustrie läuft die Suche nach effizienten Technologien auf Hochtouren. Ric Parker, Chefentwickler des Triebwerksbauers Rolls-Royce, über Keramikfasern, Riesenfans und den guten alten Propeller.

Foto: Rolls-Royce
VDI nachrichten: Herr Parker, die Flugzeugbauer prognostizieren, dass die Fluggastzahlen bis 2032 jährlich um 5 % zunehmen …
Ric Parker: … ich glaube sogar, sie nehmen bis 2050 so stark zu. Ich sehe nicht, dass diese Entwicklung abreißt.
Kann ein solches Flugaufkommen überhaupt umweltverträglich sein?
Wir haben gemeinsam mit vielen anderen Luftfahrtunternehmen den „Flightpath 2050“ erarbeitet, einen Bericht an die Europäische Kommission, in dem wir uns Ziele setzen, damit wir nachhaltig wachsen können.
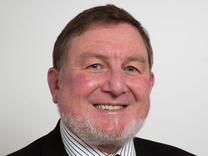
Wie lauten diese Ziele?
Verglichen mit einer Boeing 777 aus dem Jahr 2000 wollen wir bis 2050 die CO2-Emissionen pro Passagier und Kilometer um 75 % verringern. Die Stickoxid-Emissionen sollen um 90 % sinken.
Aber es werden doch auch immer mehr Flugzeuge fliegen …
Es stimmt, das Verkehrsaufkommen in der Luft dürfte sich – gerechnet von 2000 bis 2050 – verachtfachen. Trotzdem glauben wir, dass sich die Menge des tatsächlich ausgestoßenen CO2 halbieren lässt.
Noch mal die Frage: Was macht Sie zuversichtlich, dass das künftige Flugaufkommen umweltverträglich sein kann?
Das Bewusstsein der Fluggäste macht mich zuversichtlich. Sie haben einen hohen Anspruch an ihre eigene Mobilität, aber eben auch den immer stärkeren Wunsch, umweltverträglich zu fliegen. Und wir haben die Möglichkeiten, effizienter zu werden – ob im Verkehrsmanagement rund um die Flughäfen oder in den technischen Details unserer Produkte durch fortlaufende Innovation …
… womit wir in Ihrem Metier angekommen sind.
Unser neues Triebwerk für den Airbus A350, die Trent XWB, stößt bereits 15 % weniger CO2 aus als ein vergleichbares Triebwerk aus dem Jahr 2000. Wir verbessern die Effizienz unserer Triebwerke um mehr als 1 % pro Jahr. Im Hinblick auf die Ziele bis 2050 sieht das gut aus.
Welche Rolle spielen in der Triebwerksentwicklung neue Materialien?
Der technologische Fortschritt in der Luftfahrt war immer stark von den vorhandenen Materialien abhängig. In der Triebwerksentwicklung ist das nicht anders. Wir brauchen neue Hochleistungswerkstoffe, um den Anforderungen gerecht zu werden – höhere Drücke und Temperaturen bei geringerem Bauteilgewicht.
Was trauen Sie den kohlenstofffaserverstärkten Kunststoffen zu?
Für unsere nächste Triebwerksgeneration, die ab 2020 flugbereit sein soll, entwickeln wir bereits einen Fan aus Carbon und Titan. Der Großteil der Turbinenschaufeln wird aus Carbon bestehen, damit wir Gewicht einsparen können. Schließlich werden die Triebwerke und damit auch die Fans immer größer. Zur Verstärkung werden die Blattspitzen aus Titan sein, denn dieses Metall ist für sein geringes Gewicht sehr steif. Zusätzlich wird die Triebwerksverkleidung, die eine gebrochene Schaufel im Falle eines Falles auffängt, künftig aus Carbon gefertigt. Wir sehen aber auch Anwendungen für Keramik-Keramik-Verbundmaterialien …
Keramik-Keramik?
Silikon-Carbidfasern in einer Silikon-Carbidmatrix. Daraus könnten wir einige der Komponenten in den heißen Bereichen des Triebwerks herstellen, für die wir heute Metall verwenden.
Welche Komponenten werden das sein?
Rund um die Turbine befinden sich statische Mantelsegmente, die verhindern, dass heißes Gas entweicht. Heute werden sie aus einer sündhaft teuren einkristallinen Nickellegierung hergestellt. Demnächst werden wir sie aus Keramik-Verbundmaterialien fertigen, deren Dichte bei einem Fünftel der Metalllegierung liegt.
Für dynamisch belastete Bauteile sind diese Keramikmaterialien also nicht vorgesehen?
Nicht in nächster Zeit, auch wenn das Fernziel durchaus darin besteht, rotierende Turbinenschaufeln daraus zu machen.
Wann werden sich die Keramikmaterialien im Flugzeug wiederfinden?
Die Mantelsegmente werden wir bereits in späteren Versionen unseres Trent-XWB-Triebwerks verbauen. Wir testen sie, während wir uns hier unterhalten. Dynamisch belastete Keramikbauteile sehe ich nicht vor 2030 in Flugzeugen.
Es scheint, als würden nicht allzu viele Metalle im Triebwerk übrig bleiben.
Der Schein trügt. Bei den Metallen sind wir noch lange nicht am Ende. Beispiel Titan-Aluminid: Das ist ultraleicht und zudem temperaturbeständig. Wir könnten die großen Schaufeln weiter hinten in der Turbine, wo es noch nicht so heiß ist, daraus fertigen und Gewicht gegenüber heutigen Nickellegierungen einsparen.
Sie haben angedeutet, dass Sie die Temperatur im Kerntriebwerk künftig steigern wollen. Brauchen Sie dafür neue Kühlkonzepte?
Der Trick besteht darin, die Kühlung auf ein Minimum zu beschränken. Zum Beispiel arbeiten wir an Kühlkanälen im Innern der Bauteile.
Setzen Sie auf additive Fertigungsverfahren, um Bauteile mit solchen Kühlkanälen herzustellen?
Definitiv, wobei das bei Turbinenschaufeln noch lange dauern kann. Die Belastungen im Betrieb erfordern einkristallines Metall und das lässt sich mit 3-D-Druck-Verfahren nicht herstellen. In unserer eigenen Entwicklung nutzen wir 3-D-Druck bereits sehr häufig.
Rolls-Royce investiert derzeit stark in Entwicklungsstätten für einen neuen Riesenfan, der alle heutigen Fans in den Schatten stellen würde. Was versprechen Sie sich davon?
Mit dem „Ultrafan“ – das ist das Riesentriebwerk, das wir gerade entwickeln – verbrauchen wir, verglichen mit heute, abermals 10 % weniger Treibstoff, verglichen mit den ersten Trent-Triebwerken sogar 25 %.
Wie groß kann ein Fan werden?
Der Fan kann nicht beliebig groß werden. Grundsätzlich ist der positive Effekt, dass ein größerer Fan mehr Schub erzeugt. Weil aber das Triebwerksgewicht und der Luftwiderstand dadurch zwangsläufig zunehmen, kommen wir an den Punkt, an dem sich Vor- und Nachteile die Waage halten. Größer zu bauen macht keinen Sinn.
Wenn Sie einmal voraussetzen, dass Ihnen all Ihre Wunschmaterialien zur Verfügung stehen und Ihre Pläne mit dem Riesenfan aufgehen – wo liegt die Effizienzgrenze in der heutigen Flugzeugkonfiguration?
Sie meinen Rumpf, Flügel, zwei Triebwerke, diese Konfiguration?
Ja. Wie effizient könnten Sie werden?
Ich glaube, dass wir uns den vorhin angesprochenen Emissionszielen nähern können, erreichen werden wir sie mit der heutigen Flugzeugkonfiguration nicht.
Wie dann?
Wir haben sehr viel zu offenen Rotoren geforscht und können uns vorstellen, dass die ab 2030 den Weg in die Flugzeuge finden.
Propeller? Aber die gibt es doch bereits …
Wir haben uns nicht aus Effizienzgründen von der Propellertechnik verabschiedet, sondern weil das Flugzeug damit nicht hoch und nicht schnell genug fliegen konnte. Mit heutiger Antriebstechnik wäre beides kein Problem mehr. Nimmt man gegenläufig drehende Propeller, winken uns sogar weitere 10 % Effizienz beim Treibstoffverbrauch, denn das Gewicht und der Luftwiderstand der Triebwerksummantelung fallen weg.
Was spricht dagegen, diese Technik bereits heute einzusetzen?
Die Ummantelung fängt nicht nur eine abgebrochene Turbinenschaufel ab, sondern sie schirmt auch den Lärm des Triebwerks ab. Wenn es darum ginge, das leisestmögliche Flugzeug zu entwickeln, bliebe der offene Rotor ein ewiges Tabu. Wobei wir laut unseren Tests die heutigen Lärmbestimmungen sogar einhalten könnten. Auch 10 dB weniger wären machbar.
Wie das?
Um das zu beantworten, müssten wir tief in die Strömungsmechanik eintauchen. Es geht zum Beispiel darum, dass die Verwirbelung der Luft aus dem vorderen Rotor den gegenläufig drehenden hinteren Rotor nicht trifft. Fakt ist aber: 20 dB weniger Triebwerkslärm – sollten die gefordert werden – wären mit offenen Rotoren nicht mehr machbar.
Grundsätzlich glauben Sie aber an völlig neue Wege in Flugzeugtechnik?
Gemeinsam mit Airbus und der Nasa arbeiten wir am „Blended Wing Body“, also an einem Flugzeug mit übergangslosem Rumpf. Und Airbus hat auf der Luftfahrtmesse ILA eine Studie des elektrisch angetriebenen „E-Thrust“ ausgestellt – ebenfalls eines unserer Gemeinschaftsprojekte. Dabei versorgt eine Gasturbine mehrere verteilte Fans mit Elektrizität. Beide Konzepte sind von heutigen Flugzeugen deutlich zu unterscheiden, werden aber vor 2030 nicht auf den Markt kommen.
Wird der Ultrafan – geplant für 2025 – überhaupt unter heutige Flugzeugflügel passen?
Er müsste sehr eng an der Tragfläche angebracht werden, aber selbst dann bräuchte es neue, höhere Fahrwerke für das Flugzeug. Die Alternative wäre, dass das Triebwerk auf der Tragfläche oder hinten auf dem Flugzeug befestigt ist. Wir befinden uns darüber in Diskussionen mit den Flugzeugbauern. Der erste Schritt ist aber, zu schauen, wie nah wir an die Tragfläche herankommen. Die Herausforderung liegt darin, dass wir damit nicht deren Aerodynamik beeinträchtigen wollen.
Wenn das Triebwerk über der Tragfläche angebracht ist, komplizieren sich Inspektion und Instandhaltung.
Das stimmt, und darum müsste der Ultrafan nicht nur ultragroß, sondern auch ultraverlässlich sein. Andererseits gibt es den positiven Effekt, dass das Flugzeug selber den Lärm nach unten abschirmt. Wir sind vom Ultrafan überzeugt, sonst würden wir nicht akzeptieren, dass wir zwischen dem Fan und dem Kerntriebwerk wegen der unterschiedlichen Betriebsdrehzahlen ein Getriebe verbauen müssen.
Rolls-Royce investiert in Dahlewitz massiv in einen Prüfstand für das Getriebe, Sie suchen derzeit 200 Ingenieure … Sind Sie sich so sicher, dass Airbus und Boeing den Fan haben möchten?
Wir haben mit beiden gesprochen und beide wissen, dass die Vergrößerung der Triebwerke der logische Schritt für Effizienzsteigerungen ist, wenn man die Flugzeugkonfiguration nicht anpacken will.
Dann gehen Sie also massiv in Vorleistung …
Unsere Entwicklungszyklen sind in der Regel etwas länger als die der Flugzeugbauer, ja.
Ihr Entwicklungsbudget hat 2013 1,1 Mrd. £ betragen, also rund 1,35 Mrd. €. Werden Sie das aufstocken?
Es kann jedenfalls nicht sinken. Wir müssen weiter investieren, um wettbewerbsfähig zu bleiben.
Der Rolls-Royce-Konzern stammt aus Großbritannien. Welche Rolle spielt für Sie Deutschland?
Eine große, das zeigen die Investitionen in Dahlewitz, wo das Zentrum von Rolls-Royce für mechanische Test ist. Aber wir betreiben noch einen weiteren Standort in Oberursel. Zudem arbeiten wir mit vielen Hochschulen und Forschungsinstituten zusammen; wir nutzen zum Beispiel den Höhenversuchsstand der Universität Stuttgart.