In einer neuen Gewichtsklasse
Stratasys und HP zählen zu den Champions, wenn es um die additive Fertigung mit Kunststoffen geht. Nun steigen beide Firmen in den Ring, um den Metallbereich zu erobern.

Foto: HP
Branchenkenner reiben sich ungläubig die Augen: Das Unternehmen Stratasys kündigt an, die additive Fertigung von Metallteilen „in eine neue Ära“ zu führen. Das ist ungefähr so, als würde Autobauer Daimler behaupten, künftig die Weichen im Schienenverkehr zu stellen. Bisher ist Stratasys nämlich vor allem für seine Kunststoffdrucker und die zugehörigen Materialien bekannt.
Haben die Entwickler aus Israel und den USA den Mund also etwas zu voll genommen? Das bleibt abzuwarten. Ihr innovatives Druckverfahren wird nicht vor Ende nächsten Jahres am Markt debütieren. Zuvor dürfen nur ausgewählte Nutzer Erfahrungen sammeln. Sie sollen anschließend Feedback geben und so zur Optimierung der „LPM“-Technologie beitragen.
LPM steht für „Layered Powder Metallurgy“. Übersetzt heißt das soviel wie „Pulverschichtmetallurgie“. Was sich dahinter verbirgt – und wie es funktioniert –, erklärt Produktmanager Rafie Grinvald: „Im ersten Schritt wird eine Schicht Metallpulver im Bauraum ausgebracht. Anschließend nutzen wir unsere PolyJet-Technologie, um die Konturen des gewünschten Bauteils hochpräzise in das Pulver zu zeichnen.“ Als Tinte fungiere eine spezielle Mischung aus Wachs und Polymer – die „Thermal Ink“.
Vor jeder weiteren Schicht aus Metall und Tinte wird das Pulverbett hydraulisch komprimiert. „Damit erhöhen wir die Dichte“, so Grinvald. Nach Abschluss der Schichtbildung wird der gesamte Inhalt des Bauraums kaltisostatisch gepresst. Danach liege die Dichte der Bauteile bereits bei 96 % bis 98 %.
Im folgenden Schritt wird die konturgebende Tinte in einem Ofen verdampft. Übrig bleiben die Bauteile und das sie umgebende Stützmaterial. Letzteres lässt sich leicht abbrechen oder automatisch abrütteln. Möglich wird das durch Sollbruchstellen. Diese wurden zuvor von einer eigens entwickelten Software automatisch generiert und mittels der Thermal Ink im Pulverbett skizziert.
Am Ende des Produktionsprozesses wartet erneut ein Ofen auf die Bauteile. „Wir sintern bei 600 °C“, so Grinvald. „Anschließend liegt die Dichte bei 99,95 %“.
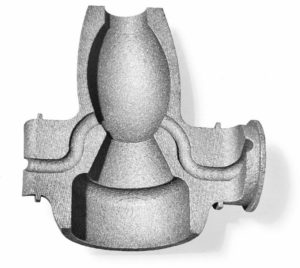
Potenziell nachteilig an dem Verfahren ist der relativ große Anteil an Stützmaterial – schließlich wird stets der gesamte Baurauminhalt hydraulisch verdichtet und kaltisostatisch gepresst. Je nach Bauteilgeometrie und -anordnung muss also viel Material abgebrochen werden. „Es lässt sich theoretisch aber sehr leicht recyceln“, entgegnet Grinvald. Unter Wirtschaftlichkeitsgesichtspunkten sei das aber nicht erforderlich. „Wir benötigen kein teures Spezialpulver, wie es beispielsweise in Lasersinteranlagen eingesetzt wird. Uns genügt günstiges Standardmaterial.“
Anfangs will sich Stratasys auf die Verarbeitung von Aluminium beschränken. „Einer Ausweitung auf weitere Metalle steht aber nichts im Wege“, so Grinvald. In der Pipeline seien u. a. Edelstahl und Kupfer.
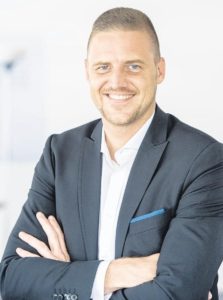
Andreas Langfeld, bei Stratasys für den EMEA-Raum verantwortlich, ist überzeugt: „Mit unserer neuen Technologie werden wir 80 % günstiger sein als der Wettbewerb – bei gleichzeitiger Verkürzung der Produktionsdauer.“ Die niedrigen Kosten seien möglich durch den Verzicht auf teure Lasertechnologie sowie den Einsatz von preiswerten Rohstoffen. Den angepeilten Gerätepreis verrät Langfeld unterdessen nicht. Auch Angaben zur geplanten Bauraumgröße lässt er sich nicht entlocken.
Neben Stratasys steigt auch HP neu in den Metalldruck ein. Die Amerikaner setzen dabei auf das Binder Jetting. Das Prinzip dieses Verfahrens ist schnell erklärt: Ein Materialschlitten bringt zunächst eine Schicht feines Metallpulver im Bauraum aus. Anschließend versprühen Düsen selektiv ein Bindemittel. Es verklebt die Partikel überall dort, wo später festes Metall entstehen soll. Diese Prozessschritte werden laufend wiederholt. Schicht für Schicht entsteht so der „Grünling“. Dieser muss anschließend entbindert und gesintert werden – fertig ist das Bauteil.
HP behauptet, bis zu 630 Mio. Nanotröpfchen des Bindemittels gezielt verteilen zu können – pro Sekunde. Möglich mache das die hauseigene Multi-Jet-Fusion-Technologie, die sich im Kunststoffdruck bereits bewährt hat.
Der Bauraum des Druckers misst 43 cm x 32 cm x 20 cm. Die minimale Schichtstärke, welche die spätere Rauheit der Bauteiloberfläche maßgeblich beeinflusst, liegt nach Unternehmensangaben bei 50 µm bis 100 µm. Nach dem Sintern haben die Bauteile von HP eine Dichte von mindestens 93 %.
Das erste, verfügbare Material ist Edelstahl. Über die Open Platform von HP bekommen allerdings ausgewählte Entwicklungspartner die Möglichkeit, neue Materialien für die Technologie zu entwickeln und anzubieten.
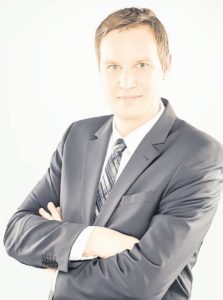
„Erste Nutzer unserer Metal-Jet-Technologie sind GKN, Siemens und Wilo“, erklärt Bastian Weimer, HP Channel Manager Germany. „Allgemein verfügbar sein wird der Drucker ab November 2019.“ Kosten soll er 399 000 €
Aktuell werden Binder-Jetting-Maschinen bereits von den Unternehmen Digital Metal aus Schweden und ExOne aus den USA vermarktet. Die Nordeuropäer haben sich auf feinste Strukturen spezialisiert. Ihre Schichtstärke liegt bei winzigen 35 µm. Demgegenüber setzen die Amerikaner mit ihren 150 µm auf eine vergleichsweise schnelle Produktion von Bauteilen.
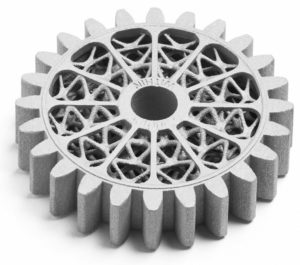
Wettbewerber Desktop Metal aus Massachusetts beeindruckt derweil vor allem mit Ankündigungen. So soll die aktuelle Entwicklung der Amerikaner mit knapp 33 000 Piezo-Spritzdüsen bis zu 60 kg Metall pro Stunde in Form bringen können – bei Schichten von nur 42,5 µm Stärke.